|
|
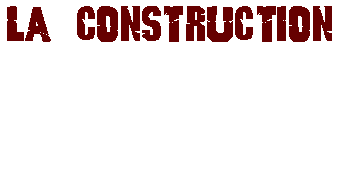 |
|
|
|
Présentation
: Pascal Delannoy |
|
|
Je vous ai présenté le Wild
; un mini-planeur DLG tout composite, facile à transporter
et à faire voler partout.
Cette deuxième partie est consacrée à la
construction tout plastique.
Une version simplifiée en balsa verni est également
proposée.
A vous de choisir la formule qui vous convient le mieux.
Bien sûr, cette méthode est applicable
à tout autre type de modèle.
|
Il ne reste plus qu’à construire le Wild.
Une petite visite chez Décathlon et vous voici en possession
d’une canne à pêche en carbone roulé pour
la pêche au coup de vitesse (modèle Speed 500 référence
3/940.691 de 2,40 m). Son prix ? 9,99 euros ! Avec une canne en trois
tronçons, il y a de quoi faire deux autres planeurs de tailles
différentes, pourquoi pas 3 Wild à différentes
échelles… Si cette référence change, il faut
simplement trouver un scion de 480 mm évoluant de 9 à
6 mm environ, solide et léger, toujours dans la gamme “pêche
au coup de vitesse” qui est une providence pour nos applications.
Pour les fournitures composites, Topmodel,
Polyplan,
proposent les matériaux employés. Pour la partie RC, AirCraft
Wold est compétitif. Enfin Conrad
propose à son catalogue les prises tulipe, le fil émaillé
d’antenne. Ensuite, c’est plus classique, une planche 80/10
de 70 g environ (pèse-lettre indispensable chez votre revendeur
!), une planche de balsa 60/10 de 50 g environ, une planche de balsa
30/10 de 30 g environ, un jonc de carbone 12/10, un autre en 10/10,
du tissu Kevlar 61 g/m² ou de verre 50 g/m², Roving 160 g/m²,
de la résine époxy lente fluide, de la cyano. Voilà
pour les fournitures principales de la version simplifiée en
balsa. Si le lancé par le saumon ne vous intéresse pas,
il suffira de faire une aile en balsa simplement vernie. C’est
la solution la plus légère et la plus rapide à
construire. Pour la version tout plastique le plan vous renseignera
avec précision. Rien de bien compliqué, un peu de styro
bleu, du ruban de carbone 125 g/m², etc. La mise sous vide vous
effraie ? Il suffit de stratifier à l’air libre et de poncer
ensuite la surface après polymérisation. Du classique
en somme. Chacun pourra utiliser la méthodologie qui lui convient.
La version tout balsa vernie est vivement conseillée pour commencer,
ensuite il est toujours possible de faire une aile tout plastique.
Avant d'entamer la stratification,
il faut tout préparer à portée de main
et dégager le plan de travail. |
Quelques conseils pour stratifier léger
- Un rouleau métallique relativement lourd permet d’éliminer
le maximum de résine des tissus.
- Un papier essuie-tout appliqué ensuite absorbe encore un peu
de résine.
- Une résine très fluide est vivement conseillée,
elle imprègne bien mieux les tissus. Une fluidité proche
de l’eau doit être recherchée.
Idéalement, une aile tout plastique de F3K de compétition
pèse 5,5 g/dm². Il est donc possible de sortir celle du
Wild à environ 70 g, avec un peu de soin. La version tout
plastique se rapprochera alors du poids idéal de 120 g.
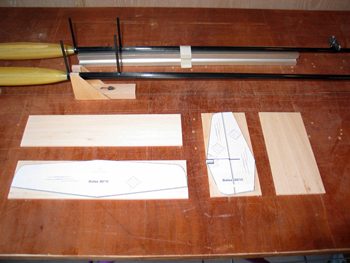
Des gabarits en carton sont utilisés pour découper
les empennages. Balsa ou Dépron, à vous de choisir.
|
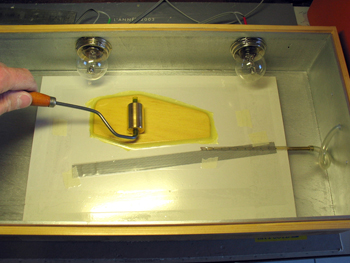
Mise sous vide en étuve. Le rouleau permet de chasser
les bulles et de lisser la surface. |
La dérive
Découper du Dépron® ou balsa 30/10, ponçage
au profil, convexe côté gauche pour les droitiers et inversement
pour les gauchers.
Stratification sous vide ou à l’air libre avec du tissu
de verre 50 g/m² ou Kevlar 36 à 61 g/m², fibres à
45°. Ou simple couche de vernis pour la version simplifiée.
Dans ce dernier cas, un peu de fil de lin collé à la cyano
autour du saumon et de la base de la dérive évite que
le balsa ne se fende au contact du sol.
Finition des bords de la version stratifiée et réalisation
de l’articulation de la dérive : Souplesse du Kevlar pour
ce type d’entoilage ou Blenderm avec le tissu de verre 50 g/m².
Si on réalise une version 2 axes ailerons/profondeur, ce travail
est évité. Voilà c’est terminé. Pose
du guignol en jonc de carbone pour la version 3 axes et chape en gaine
thermorétractable ou gaine plastique souple.
Sur la balance, la dérive pèse 3,8 g.
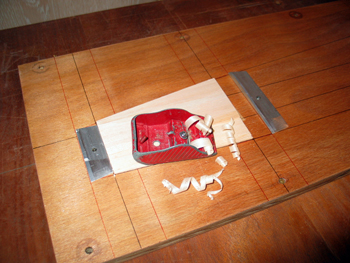
Mise en forme du stab découpé dans du balsa.
Pour commencer, on approche le profil au rabot à lame de
rasoir. |
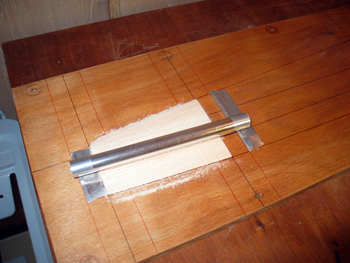
La cale à poncer est un tube alu de 20 mm sur lequel
est collé du papier de verre. Celui-ci s'arrête avant
les bords afin de ne pas déformer les gabarits.
|
Le stabilisateur
Découpe comme la dérive dans du Dépron® ou
balsa 30/10, ponçage au profil qui est plat à l’intrados
et convexe à l’extrados, donc porteur.
On insère un petit tube aluminium de 2x3x3 mm au niveau de la
fixation pour passer la quick link. Cela évite l’écrasement
au serrage.
Stratification comme pour la dérive avec les mêmes tissus
au choix, fibres à 45°, ou simple couche de verni (pour le
balsa, le Dépron® lui doit être stratifié).
Finition des bords. On fraise ensuite le logement du support de l’incidence
intégrale.
Sur la balance, un stabilisateur stratifié pèse 5 g. Moins
de 2 g pour la version vernie.
Une défonceuse est utilisée
afin de pratiquer
une rainure dans le stabilisateur. |
L’aile
Commencer par découper les panneaux au format de l’aile,
en styro bleu (Roofmat) ou balsa au choix. Découpe du profil
sur machine automatique avec poulies et poids ou CNC pour les mieux
outillés ou chez un revendeur équipé d’une
machine de ce type comme PG
Modélisme. Pour la version en balsa, simple ponçage avec
un tube alu de 20 mm sur lequel on colle au double face moquette du
papier de verre grain 80. Des gabarits en aluminium sont employés
pour les perfectionnistes…
Version mousse : collage du bord d’attaque, des longerons, du
contre-plaqué balsa 3 plis 20/10 au niveau des ailerons pour
éviter l’arrachement de la mousse sous effort. Pose de
petits tronçons de tube carbone diamètre 4 mm au niveau
des guignols et du jonc de lancement SAL.
Découpe du saumon en arrondis, pose de la nervure d’emplanture
en carbone pour la version mousse.
Stratification pour la version mousse ou balsa avec du tissu de verre
50 g/m² ou Kevlar 36 g/m², fibres à 45°. J’ai
fait un bâti incluant le dièdre. Ainsi l’aile est
faite en une fois, intrados, extrados et renfort central. Plus simplement,
il est possible de stratifier séparément chaque demi-aile
pour les assembler au dièdre prévu ensuite.
Découpe de l’aileron, articulation avec le tissu Kevlar
(donc découpe de l’intrados uniquement et ponçage
avec prudence jusqu’à atteindre l’extrados sans mordre
dans le tissu) ou découpe complète et pose de Blenderm
avec du tissu de verre ou pour la version vernie. A ce niveau, pour
la version vernie, je vous conseille vivement de coller un tube aluminium
de diamètre 3 mm proche du bord d’attaque de l’aileron.
En effet, sans tissu de verre ou Kevlar, la résistance en torsion
du balsa est insuffisante et le flutter sera immédiat sur un
lancé SAL moyen. Deux tubes carbone de 6 mm sont collés
bien verticalement avec le fuselage terminé comme guide. Ils
assurent le maintien de l’aile. Le collage se fait à l’époxy
lente genre Araldite.
Pose des servos d’ailerons et des guignols. Les commandes sont
réalisées en Inox 8/10 de pêche plié en “Z”
côté servo. La chape est en gaine thermo ou gaine souple
plastique. La prise centrale tulipe ou équivalent sera collée
par la suite, lorsque le fuselage sera terminé. C’est important
pour obtenir un montage parfait des prises entre elles et donc un contact
fiable.
Sur la balance, une aile Kevlar 61 g/m² pèse 84 g, une aile
balsa stratifiée tissu de verre 50 g/m² poncée sans
mise sous vide 83 g, une aile en balsa vernie 55 g.
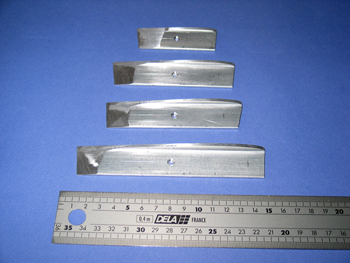
Des gabarits ont été taillés dans de la cornière
en en AU4G pour poncer l'aile de la version bois en balsa plein.
|
Un
tube alu recouvert d’abrasif grain 100 vient en appui sur
les gabarits. On voit ici les différentes épaisseurs
de balsa. |
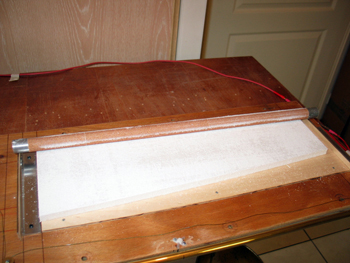
Même procédé pour rattaper les éventuels
défauts de surface sur un noyau en polystyrène découpé
au fil chaud. |
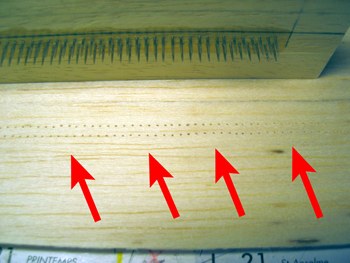
Gros plan du perçage anti délaminage
de l'articulation sur l'aile
en version balsa plein. |
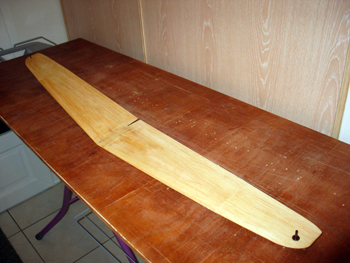
L'aile du Wild en balsa stratifié après
ponçage : simplicité et légèreté.
|
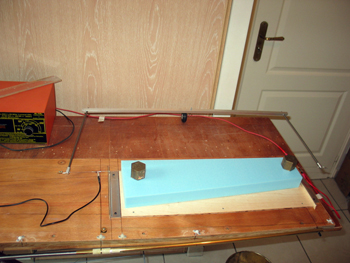
Plus classiques : les noyaux en extrudés découpés
au fil chaud sur une machine semi-automatique. |
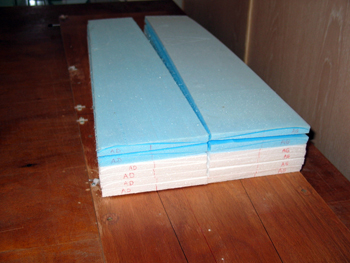
On découpe 2 ailes dans un pain de 50 mm d'épaisseur
! |
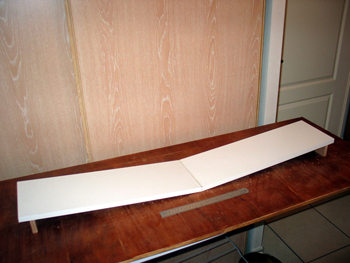
Une étagère transformée en moule
incluant
le dièdre, afin de réaliser la stratification de
l'aile d'une pièce. |
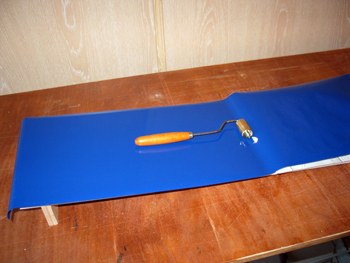
Application du Venylia au rouleau ébulleur.
|
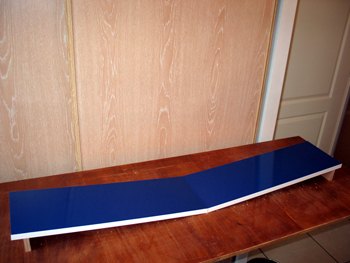
Le moule d'aile est terminé. |
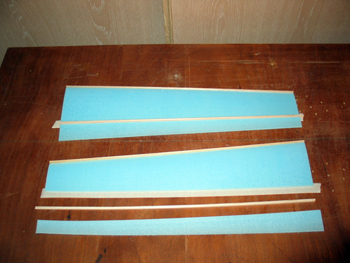
Collage du bord d'attaque et du contre-plaqué de
balsa au niveau de l'aileron. |
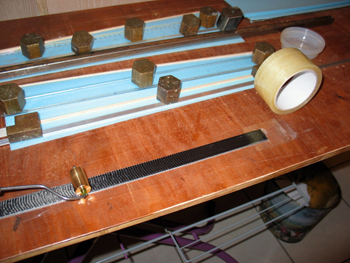
Stratification du carbone sous scotch transparent dans
lequel seront découpés les longerons. |
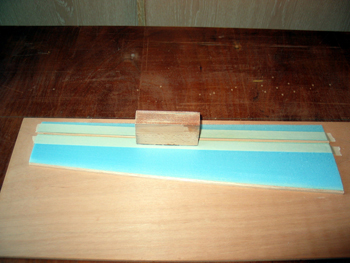
Ponçage du longeron arrière. Le ruban adhésif
protège le noyau des coups de poncette.
|
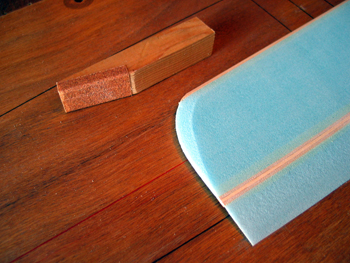
Ponçage du saumon avec une cale à 15°.
|
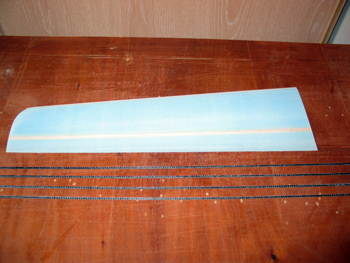
Découpe des 4 longerons de 3 mm en carbone.
|
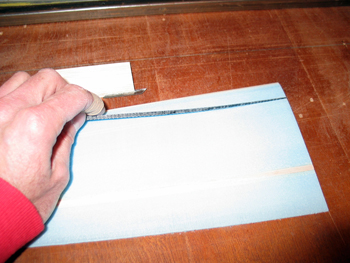
Pose des longerons dans un trait de scie. |
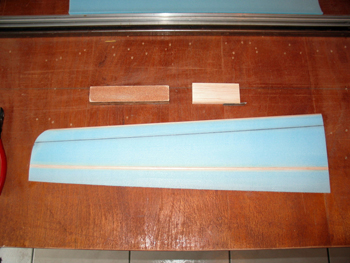
Les longerons en place, un dessus, l'autre dessous.
|
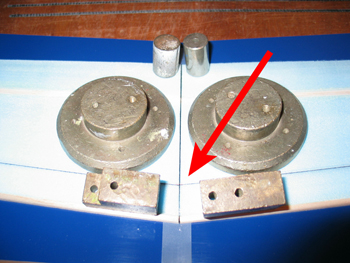
Collage des demi-ailes, notez la nervure en carbone. Les longerons
doivent tomber en face. |
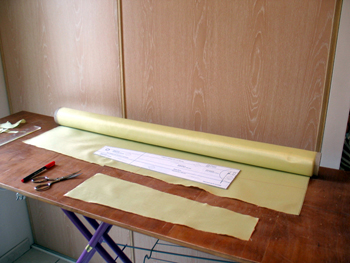
Découpe du tissu de Kevlar avec un gabarit
en carton. |
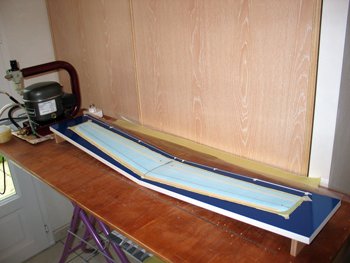
Stratification en deux étapes : on commence par l'intrados.
|
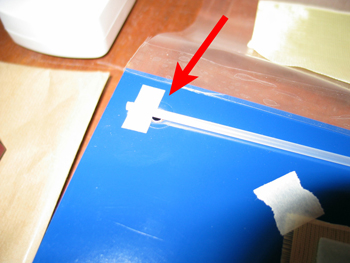
Mise sous vide
avec une gaine souple. |
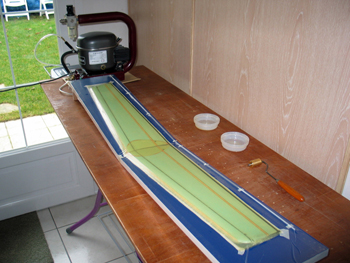
Le vide est obtenu avec un compresseur d'aérographe branché
en aspiration. |
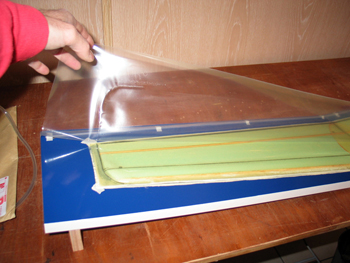
Le film plastique doit être bien tendu.
Démoulage après polymérisation. Ca brille...
|
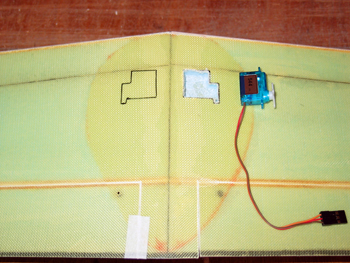
Découpe du logement des servos à l'intrados.
|
Le fuselage
Pour terminer l’aile, il faut disposer du fuselage ou tout au
moins de la poutre arrière en carbone avec les deux tubes carbone
de 4 mm servant à la fixation très rigide de l’aile.
Tronçonner le scion intermédiaire de la canne à
pêche à 580 mm de long (on le coupe du côté
du plus petit diamètre). Monter une fraise diamantée sur
une mini perceuse genre Dremel tournant au moins à 15 000 rpm.
Fraiser le passage de la prise tulipe ou autre prise équivalente
avec au minimum 4 contacts. Fraiser à 4 mm les emplacements des
tubes carbone de fixation d’aile et terminer par le passage de
la quick link du stabilisateur. Tout ce travail est fait avec une perceuse
à colonne miniature pour rester bien vertical et centré.
Collez à l’époxy lente genre Araldite mélangée
à de la fibre broyée les tubes carbone bien droits et
parallèles. Présenter alors l’aile pour coller la
prise servos et les tubes carbone diamètre 6 mm extérieur
permettant l’assise de l’aile.
Le “V” du stabilisateur est moulé en carbone dans
une forme en contre-plaqué de 150 mm et serré pendant
la polymérisation de la résine. Du scotch d’emballage
sert de démoulant.
La platine supportant le stabilisateur est moulée sur une cornière
aluminium. Toujours avec du scotch d’emballage comme démoulant.
Le “V” est collé avec l’aile montée
comme référence, bien parallèle et perpendiculaire
au fuselage.
On colle la dérive avec un renfort en tissu 80 g/m². On
présente le stabilisateur et sa platine avec des languettes de
tissu Kevlar servant d’articulation. Une fois que tout est bien
parallèle, on colle à la cyano le Kevlar sur le “V”.
On dépose ensuite l’aile.
Il faut maintenant tourner un rond en hêtre de 30 mm à
la forme de l’ogive. Un pied de mobilier tout fait, proche de
la forme idéale, pourra sûrement se trouver dans les GMS
de bricolage. Une planche de 19 mm en mélaminé blanc est
découpée à la forme extérieure de l’ogive.
Une gaine thermo est appliquée sur l’ogive pour servir
de surface lisse et la protéger en même temps. On colle
l’ogive bien au centre sur le mélaminé. Du Sintofer
est appliqué au plan de joint. Deux couches de démoulant
à base d’alcool polyvinylique sont appliquées à
l’aérographe. Ensuite, c’est classique, gel coat,
tissu de verre fin puis couches de Roving 160 puis 400 g/m² pour
constituer un moule faisant environ 5 mm d’épaisseur. Ebarbage
et démoulage, cela brille !
Stratification de l’ogive, tissu de verre à 45° Roving
160 g/m² et en surface (première couche dans le moule) Kevlar
61 g/m² toujours à 45°. Etuvage à 45°C. Démoulage
ébarbage. On recommence pour faire la deuxième coquille.
Celle-ci est ouverte à la forme de la verrière avec une
fraise diamantée. Ponçage fin des bords 400, 600 puis
1200 pour venir à bout des fibres de Kevlar. Les deux coquilles
sont rassemblées par une bande de tissu Kevlar 61 g/m².
Un ruban de Blenderm entoure la jointure pour éviter que la résine
coule sur la surface extérieure et maintient l’ensemble
pendant la polymérisation si possible en étuve à
35 ou 40° C. C’est terminé ! Une version simplifiée
pourra se contenter d’une simple platine en contre-plaqué
balsa + fibre comme sur un avion RC avec les servos, le récepteur
ensuite protégés par une gaine thermo moulée sur
une forme. C’est plus rapide mais moins esthétique ! Poids
de l’ogive terminée 10 g. Résistance à toute
épreuve…
On colle l’ogive bien dans l’axe du tube carbone, éventuellement
sur un bâti. Résine époxy lente et fibre broyée
sont indispensables pour ce point névralgique. Cette ogive pourra
avantageusement servir sur un planeur de 1,50 m ou plus. C’est
un peu un investissement à long terme en quelque sorte, d’où
l’intérêt de soigner le moule !
On monte les servos sur des joncs carbone 15/10. Les vis des servos
de 4 ou 5 g Cortex, Dymond, HES Electronics, Jamara (même produit
mais plusieurs distributeurs !) viennent se prendre dans le jonc, le
montage est sans jeu et sans trous à percer ! On passe les commandes,
on règle les neutres et débattements suivant le plan.
L’accu est un Li-Po 145 mA Kokam de 3,7 volts, autonomie 1 h 30
en version 2 axes et 1 heure en version 3 axes avec 4 servos. Les servos
et les récepteurs pour park flyer fonctionnent bien jusqu’à
3 volts. Choisir un récepteur 6 voies dotée d’une
portée au sol de 300 m minimum (Schulze Alpha 840, GWS 6 voies,
etc.). Le fil d’antenne est remplacé par 2 fils émaillés
torsadés ensemble, la longueur totale restant identique. 1,5
g de gagnés sur ce poste ! Laisser pendre dans le vent au moins
30 cm de fil pour éviter les pertes de portée, le tube
carbone est perturbateur pour nos ondes radio. Le fil est scotché
à l’extérieur du tube.
On termine en montant le stabilisateur et l’aile. Il faut maintenant
vérifier le centrage. Si on a bien travaillé, 5 g maximum
de lest sont nécessaires avec un récepteur de 10 g.
La verrière en gaine thermorétractable transparente est
rétractée sur l’ogive en hêtre qui nous sert
à nouveau, poids 0,5 g. Elle est maintenue avec du Blenderm.
Le Wild sur la balance pèse un peu plus de 150 g pour la version
tout plastique et s’approche des 120 g pour la version avec aile
en balsa verni non destinée au lancement SAL.
Pour les perfectionnistes, une housse avec 3 compartiments, un pour
l’aile, un autre pour le fuselage et un dernier pour le stabilisateur
et les accus, de 20x105 cm sera bienvenue pour le transport. Une sangle
est cousue pour un maintien parfait sur un deux roues ou en randonnée.
Le master de l'ogive du fuselage
en hêtre a été mis en forme sur un tour.
|
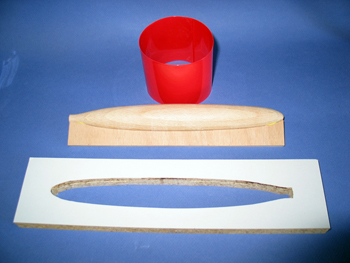
La forme immobilisée sur son
support, la gaine et le plan de joint en mélaminé.
|
La finition de l'ogive est simplement
assurée avec un morceau de gaine thermo.
|
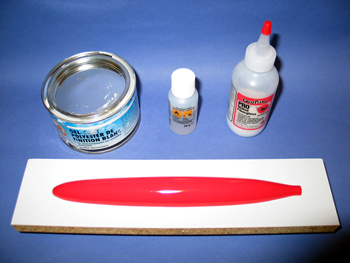
L'ogive en place dans le mélaminé.
La gaine est lustrée, la surface est parfaite.
|
Après gel coat et stratification,
le moule est prêt, sans défauts.
|
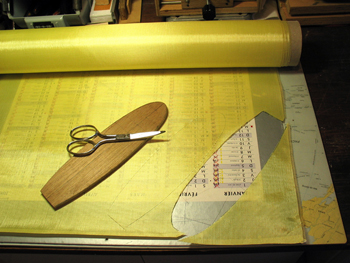
Le tissu de Kevlar est coupé
à 45° pour épouser les formes, en s'aidant d'un
gabarit. |
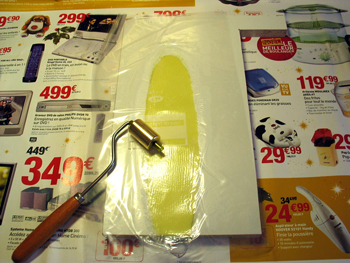
Le tissu est passé au rouleau
métallique pour chasser les bulles et le surplus de résine.
|
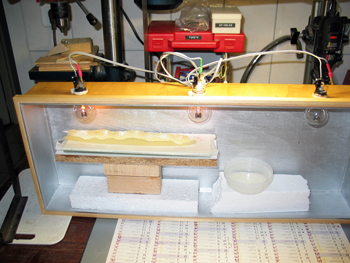
Etuvage avec des ampoules auto 12
V pour favoriser la polymérisation. |
Les demi-ogives dont les bords ont
été ébarbés sont sorties du moule.
|
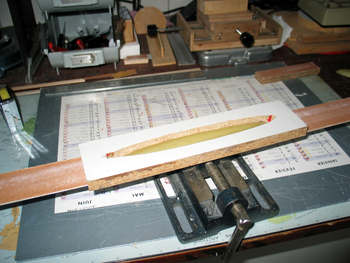
Ponçage plan des demi-ogives
en s'aidant du chantier pour les maintenir.. |
Collage à la colle contact
des bandes renforts. On voit l'ouverture fraisée dans la
partie haute. |
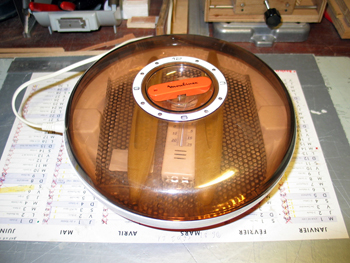
Etuvage de deux ogives fermées
dans une yaourtière. |
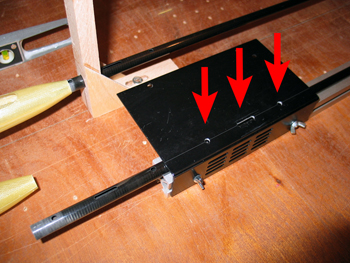
Gabarit de perçage du tube
de queue.
Le perçage
demande de la précision.
|
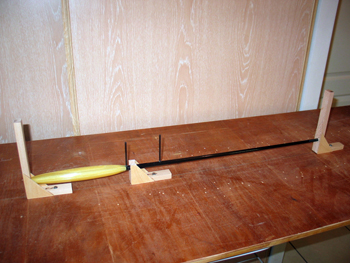
Collage axé de l'ogive sur
un bâti vissé. |
Profilé alu pour mouler la
platine du stab. |
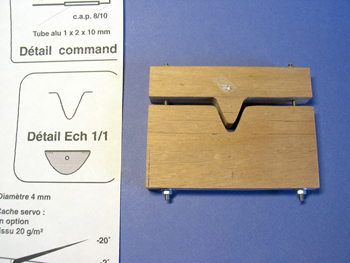
Forme en contre-plaqué 15
mm du support de platine. |
Du ruban adhésif sert de
démoulant pour le support de la platine.
|
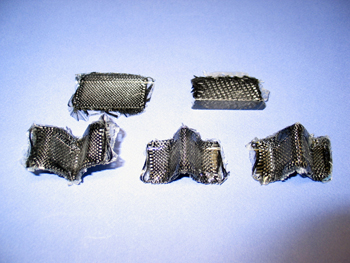
Les pièces du stab au démoulage.
|
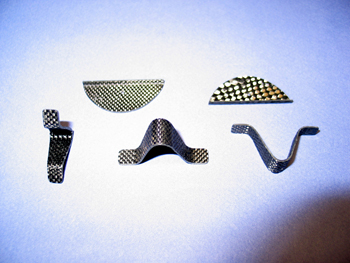
La platine et son support terminés.
|
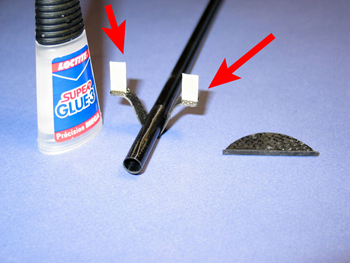
Du tissu de Kevlar 200 g/m2 est collé pour l'articulation
de la platine. |
Ouverture fraisée dans la
poutre pour la commande de la platine. |
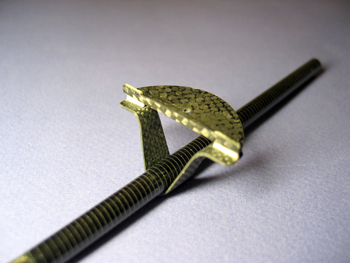
Pointage à la cyano du support
sur les bandes de Kevlar. |
Tube souple de pêche et quick
link usiné à 1 mm pour la commande de prof.
|
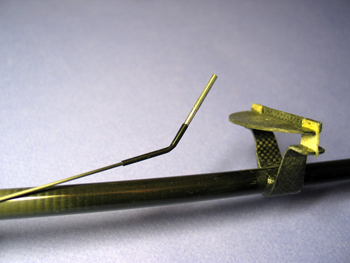
La commande de profondeur terminée.
|
Le support de stabilisateur achevé.
|
Les réglages
Voici un chapitre à ne pas négliger, aucun jeu, pas de
vrillage nuisible au vol et une optimisation du centrage sont à
respecter impérativement. Le plan vous donne toutes les valeurs.
Les respecter pour les premiers vols. Le centrage sera à affiner
avec le stabilisateur bien horizontal par rapport à la ligne
de vol et non par rapport au dessus du tube carbone qui est conique
donc en pente ! Ensuite centrer le Wild pour obtenir le plané
le plus long possible sur un lancé main classique, le stabilisateur
restant sur ce réglage de base. La valeur du plan en est proche.
Contrôler la portée radio antenne sortie, si c’est
une antenne courte que vous utilisez à l’émetteur,
vous perdez 30% environ. Avec un récepteur Schulze c’est
sans problème, avec les autres soyez prudents… Eloignez
le fil d’antenne un peu plus ou tendez-le avec le sommet de la
dérive en cas de difficultés à obtenir une portée
correcte.
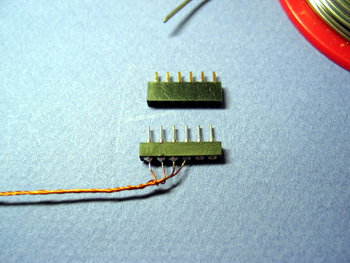
Câblage de la prise tulipe,
+ et - réunis,
signal voie 1, signal voie 2, en fil émaillé.
|
La prise tulipe mâle est collée
sur la poutre
du fuselage. |
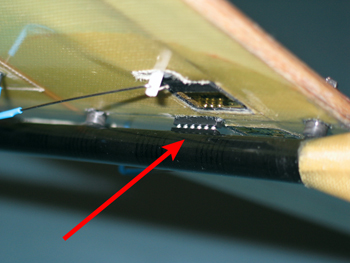
Gros plan sur la prise tulipe qui
se branche quand l'aile est mise ne place. |
Les servos sont en place ;
notez les chapes en gaine thermo. |
Sauvage…
Le Wild permet le vol sauvage, avec un véritable contact avec
la nature, son transport est presque insensible dans une housse. Si
vous vous déplacez en deux roues le Wild vous suivra partout.
Voler loin des agglomérations ou au contraire dans un parc de
loisirs, faire de la randonnée pédestre en montagne ou
dans une campagne généreusement vallonnée vous
fera découvrir de nouvelles sensations. Prenez avec vous 3 accus
Li-Po de 145 mA et vous vous amuserez pendant 3 heures… En bord
de mer, sur les dunes, sa finition plastique le rend insensible à
l’humidité. Une prise de contact un peu rude avec la planète
sera généralement indolore, la structure et le faible
poids limitent les dégâts. En montagne, avec un air moins
dense, là c’est un must, les prises de badin joufflues,
sans bruit ou presque tant la cellule traîne peu avec une voltige
incisive sont jouissives. En faisant varier la courbure, le vol évoluera
à volonté suivant votre humeur ou l’aérologie
locale. Pour finir, le plaisir de faire voler un planeur tout plastique
que l’on aura fabriqué soi-même est une autre source
de satisfaction.
Bons vols à toutes et à tous !
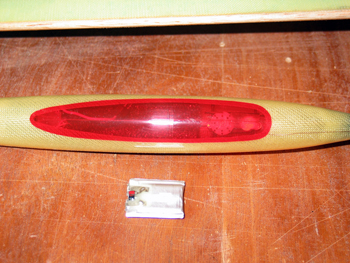
La verrière en gaine thermo
et un accu Li-Po de 145 mA 3,7 V qui permet de voler pendant
1 heure. |
Pour un lancé musclé,
l'indispensable téton en bout d'aile composé d'un
tube carbone diamètre 4 mm. |
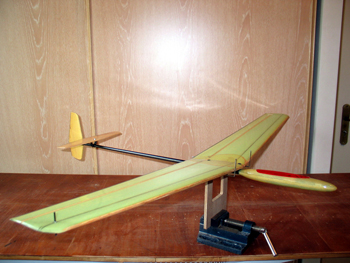
Centrage précis à 60
mm
pour le premier vol. |
Prêt pour la compétition
ou le vol de loisir très performant. |
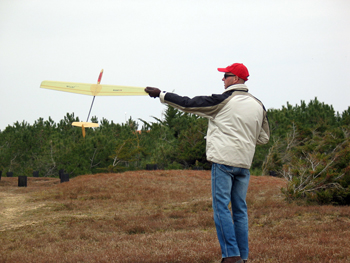
Juste avant le lâché
à 60 ou 70° de pente. |
Pour revenir
à la page de présentation du Wild, cliquer sur l'image
: |
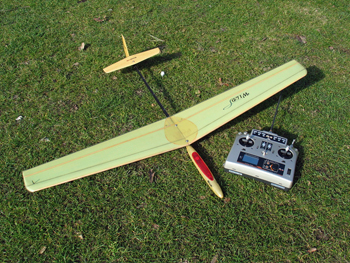 |