Imprimez une verrière !
On vous l'explique... en toute
transparence !
Texte et photos : Laurent
Schmitz
Une verrière, ou des feux de position,
des hublots, les cadrans de cockpit,… Bref, toute surface de nos
modèles qui doit être transparente. C’était
déjà faisable à l’aide d’une imprimante
3D à résine mais aujourd’hui on peut obtenir de
bons résultats avec une imprimante 3D à filament.
L’impression en résine n’est pas vraiment une bonne
option pour les modèles RC : trop petit, trop coûteux,
trop compliqué... En impression "FDM" (avec du filament)
on peut opter pour du simple PLA transparent. La pièce est alors
facile à imprimer, bon marché et relativement solide.
Mais le matériau est plus translucide que transparent. En plus,
les fines lignes des couches successives dévient la lumière
et empêchent de voir à travers. Ce problème peut
en partie être résolu en couvrant la surface (intérieur
et extérieur) avec de l’époxy fluide, mais la manip
est loin d’être évidente.
Le PETG transparent donne un meilleur résultat que le PLA mais
il est un peu plus cher et surtout bien plus difficile à imprimer,
avec des soucis d’adhérence et un risque de déformation
des pièces. En vol l’aspect est acceptable mais au sol,
on devine à peine ce qui se trouve derrière le vitrage.
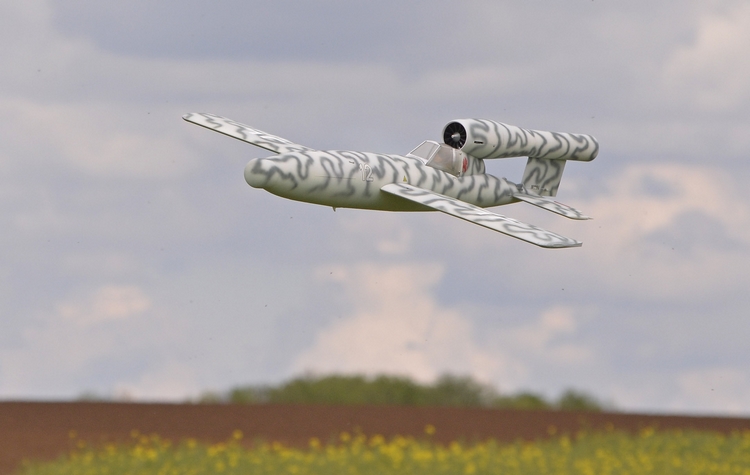 |
Canopy en PETG ou PLA transparent.
On devine le pilote à travers, c’est suffisant en
vol mais pas convainquant de plus près. |
Le PVB transparent change réellement la donne, avec la possibilité
d’imprimer de grandes verrières presque aussi belles qu’une
pièce d’origine thermoformée. J’utilise désormais
le "Polysmooth"
de la marque Polymaker.
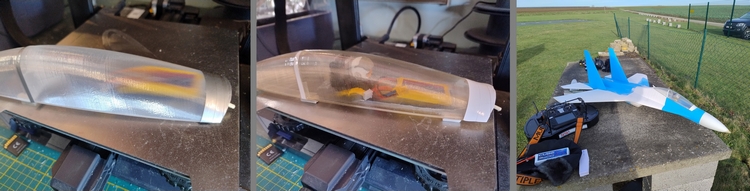 |
Verrière en PETG à
gauche, en PVB double paroi au centre et la même sur l’avion
à droite. |
L’impression de ce filament est aisée, à 190°
pour la buse et 60° pour le plateau, avec une bonne adhésion
et aucune déformation. Après avoir retiré la pièce
il faut être prudent car elle est fragile, elle risque de se délaminer
et de casser. Tout cela change après avoir enduit la verrière
d’alcool isopropylique (IPA). Celui-ci dissout le PVB, en commençant
par les petits reliefs, comme les arêtes des lignes d’impression.
Le "jus" sèche entre les lignes et comble ainsi les
interstices. Il faut vraiment bien tremper la surface, intérieur
et extérieur. Tant que le matériau est mouillé,
on peut le lisser du doigt. Un pulvérisateur à plantes
permet d’accéder facilement même dans les coins.
On suspend ensuite la pièce pour que l’excédent
en coule et on laisse sécher un quart d’heure avant de
recommencer. Quatre ou cinq traitements donnent la meilleure finition.
À ce stade, la verrière est franchement souple et souvent
laiteuse. Il faut la laisser sécher totalement. Elle peut être
manipulée après quelques heures mais il faut une semaine
au sec pour qu’elle soit à nouveau dure (ce qui permet
de rectifier les petits défauts de forme en la montant sur le
modèle). Notez que le PVB se soude facilement sur lui-même
en enduisant les parties en contact d’IPA. Ça marche exactement
comme pour les maquettes plastique.
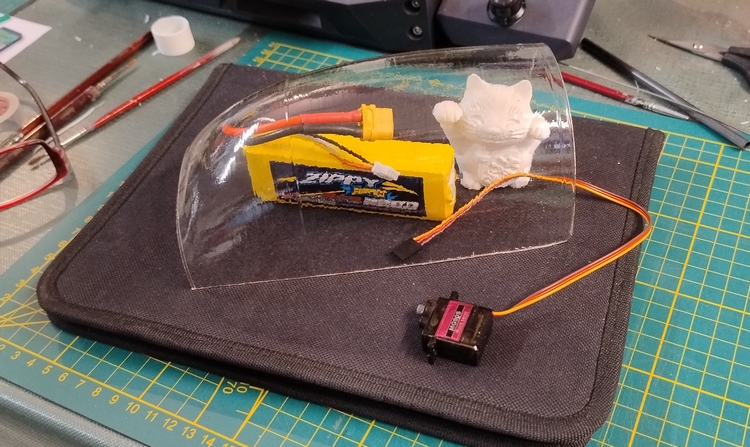 |
Simple paroi de PVB, imprimée
avec une buse de 0,8 mm puis lissée à l’alcool
: presque aussi bien qu’une verrière thermoformée
classique. |
Le traitement à l’IPA lisse la pièce mais la rend
aussi un peu plus fine. Avec une imprimante standard et une buse de
0,4 mm on peut fabriquer de petites pièces, jusqu’à
±4 centimètres avec une seule paroi (ou "périmètre").
Plus grand que ça et la pièce s’avère trop
fine et trop souple. On peut augmenter le nombre de parois mais la transparence
est moins bonne car de minuscules bulles d’air restent emprisonnées
entre les deux couches. La solution est d’utiliser une buse plus
grande. 0,8 mm convient bien pour une verrière jusqu’à
une vingtaine de centimètres et avec une buse de 1 mm la paroi
est assez épaisse pour toutes les formes imprimables sur un plateau
standard de 22x22 cm. Pour maximiser l’épaisseur on peut
pousser le paramètre "flow " jusqu’à 120%
si nécessaire. Quant à la vitesse, 50 mm/sec est un bon
compromis. La masse de la verrière terminée est comparable
à celle d’une pièce thermoformée.
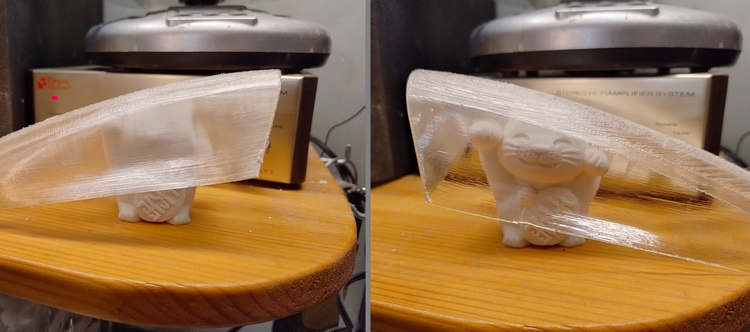 |
PVB avant et après lissage
à l’alcool isopropylique sur cette pièce ratée
(imprimée par erreur à l’horizontale). |
Le PVB Polysmooth de Polymaker existe également dans une vingtaine
de couleurs opaques. Après traitement à l’IPA il
permet d’obtenir des pièces non transparentes mais lisses
et brillantes. D’autres marques produisent du PVB transparent
teinté, par exemple pour de belles verrières de planeur
bleues, délicieusement rétro. Prusa fait même du
"fumé", pour les verrières de Jets. Je n’ai
pas encore essayé ces marques mais le principe reste le même.
Pour changer de buse, c’est très simple : montez la tête
d’impression à une quinzaine de centimètres en "Z",
retirez la coque en silicone qui couvre le bloc de chauffe puis activez
le préchauffage. Quand la température approche 200°,
retirez le filament, utilisez une pince à longs becs pour tenir
le bloc de chauffe et dévissez la buse à l’aide
d’une clé à douille de 6 mm (pour une buse MK8 standard).
Attention de ne pas vous brûler ! Inutile de forcer, la buse se
dévisse facilement. Vissez la nouvelle buse, remettez la coque
molle et coupez le préchauffage. N’oubliez pas de refaire
la procédure de mise à niveau et surtout de régler
la distance "Offset" : une feuille de papier doit tout juste
pouvoir bouger entre la buse et le plateau. Dans le programme de découpage
(Slicer), sélectionnez la nouvelle taille de buse avant de traiter
les objets. La hauteur de ligne minimale est proportionnelle au diamètre
du trou. Par exemple, si vous pouviez imprimer des lignes de 0,12 mm
avec la buse d’origine (de 0,4 mm), vous ne pourrez pas descendre
sous 0,24 mm avec une buse de 0,8 mm.
Le PVB est un des matériaux les plus hygroscopiques, il absorbe
énormément d’eau de l’air ambiant. Il est
impératif de bien le sécher avant l’emploi. Ma bobine
restée quelques jours dans mon atelier formait encore des bulles
à l’impression après 6 h de séchage à
55° dans un boîtier spécial. Lors des premières
minutes de séchage, le capot du séchoir était couvert
de gouttes d’eau ! Il a fallu six heures de séchage supplémentaires
pour imprimer correctement. Si le filament contient de l’eau,
on entend le bruit des microbulles qui éclatent et la pièce
sort translucide.
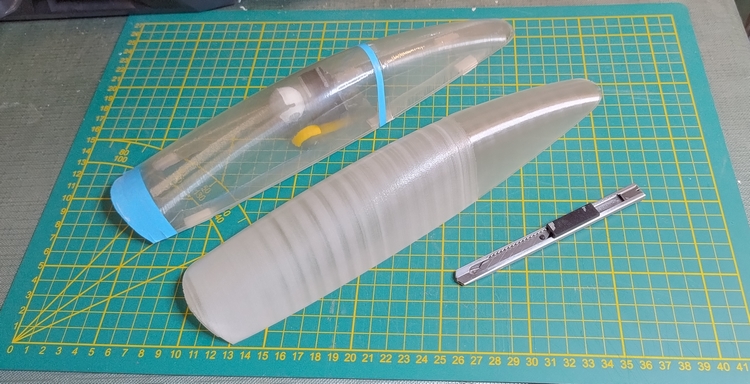 |
La verrière du bas a été
imprimée avec du filament PVB ayant absorbé l’humidité
ambiante. Elle est bonne pour la poubelle… |
Le PVB présente d’autres désavantages. Tout d’abord,
il est relativement cher. Comptez 45 € pour une bobine de 750 g,
plus 15 € pour deux litres d’alcool isopropylique. Mais pour
60 € on imprime facilement une douzaine de verrières, qui
reviennent donc à 5 € chacune. Les manipulations ne sont
pas compliquées mais durent longtemps et peuvent rebuter certains.
Le matériau présente une légère teinte fumée,
il n’est pas 100% clair. Enfin, avec une température de
transition de 60°, il craint le soleil et la chaleur. Si vous laissez
votre avion dans la voiture au soleil en été, la verrière
se déformera.
Malgré ces désavantages, le PVB offre aux aéromodélistes
la possibilité de remplacer une verrière cassée
ou perdue, introuvable dans le commerce. Et bien sûr on peut facilement
créer n’importe quel accessoire transparent. L’impression
3D s’impose donc de plus en plus comme une alternative aux techniques
traditionnelles, comme le thermoformage de verrières. Ce qui
pose un nouveau problème, car maintenant que les verrières
imprimées en 3D sont réellement transparentes, on ne peut
plus bâcler l’aménagement du cockpit.
Contact : laurent.schmitz@jivaro-models.org
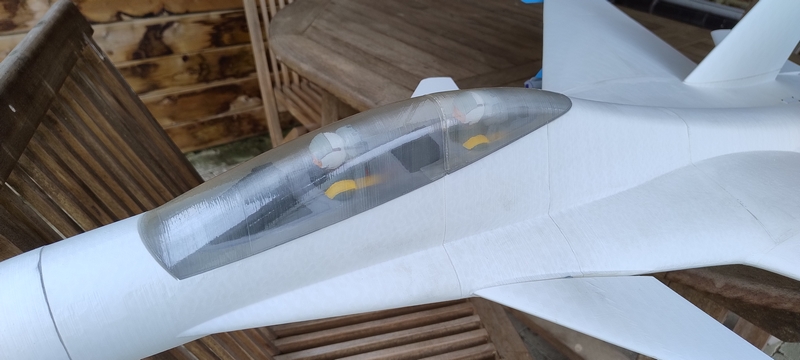 |
Pour la verrière de ce
jet rapide, j’avais opté pour une double paroi de
PVB avec une buse de 0,4 mm. La transparence est moyenne mais
le matériau est bien rigide. Depuis, j’utilise une
simple paroi mais avec une buse de plus grand diamètre. |