Imprimez votre avion !
Présentation : Laurent
Schmitz
L’impression de modèles RC en
3D existe déjà depuis quelques années mais avec
des résultats souvent incertains : matériau fragile, modèles
de petite taille, conception pas toujours adéquate et surtout
une masse plus élevée qu’un avion classique en mousse
moulée ou même en balsa. La mise sur le marché de
filaments ultralégers et les progrès tant dans les imprimantes
que la conception changent aujourd’hui la donne.
J’avais déjà vu voler un avion imprimé en
3D : un petit modèle "façon Spitfire", bien
trop lourd et aux ailes qui prenaient dix degrés de dièdre
à chaque ressource. Le premier atterrissage avait réglé
son compte à l’engin, qui s’était démantibulé
au contact de la piste. Autant dire que j’avais un petit à
priori concernant cette nouvelle forme d’aéromodélisme.
J’ai donc acquis une imprimante 3D avec l’idée de
mouler uniquement des pièces spécifiques : capots, cônes,
armement, détails, etc. Mon choix s’est porté sur
la Creality Ender-3 S1, un grand classique dans la catégorie
"pas chère supérieure". En même temps
que l’imprimante, j’ai commandé du PLA "moussant"
de chez 3DLabPrint
en 1,75 mm de diamètre. Ce filament baptisé "PolyLight"
a la particularité de gonfler à partir de 230 degrés.
Comme il s’étend, il en faut moins pour un même volume
d’impression. Le fabriquant annonce une masse fort réduite,
jusqu’à la moitié d’un PLA traditionnel. 3DLabPrint
recommande le programme "slicer" payant Simplify3D mais donne
des indications pour ceux qui préfèrent Cura, le logiciel
gratuit le plus courant et que j’ai choisi.
PolyLight de 3DLabPrint : mes réglages
pour Cura
- PolyLight 3DLabPrint
- Quality: Layer Height = 0,24 mm
- Material: Print = 230°, Bed = 56°, Flow =
65 %
- Speed: 25 mm/s
- Cooling: OFF
- Travel: Enable Retraction = OFF
- Vase mode: Special Modes = Spiralize
|
Comme j’ai trouvé tout
un tas de charges externes et de bombes à l’échelle
sur "Thingiverse", je me lance dans l’impression
en PolyLight (abrégé "LW" pour "Light
Weight") de missiles Sidewinder.
Ma fille m’en avait déjà sorti en PLA classique
sur son imprimante, ce sera l’occasion de comparer la masse
et la finition.
Faute classique de débutant, je charge le plateau avec
les deux pièces du missile plus une munition antiradar
"Shrike", croyant optimiser le temps d’impression...
Le matin je découvre les pièces entourées
de cheveux d’ange un peu partout, là où la
buse a voyagé d’un objet à l’autre. |
 |
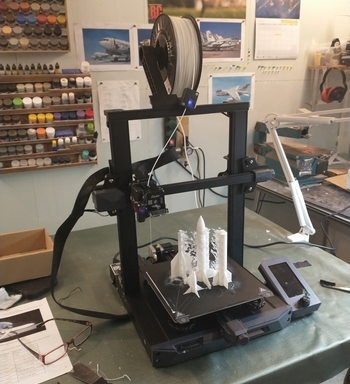 |
Le filament LW continue à sortir de lui-même tant que
la buse est chaude, même quand le moteur d’alimentation
est coupé. Il est donc préférable d’imprimer
pièce par pièce sinon le nettoyage est fastidieux, on
perd du filament et la finition est moins bonne. Malgré ma bourde,
après ébarbage le résultat est bluffant ! Le missile
ne pèse que 8 grammes contre 20 pour la version en PLA. Le nouveau
Sidewinder est pourtant un peu plus grand que le précédent.
Cerise sur le gâteau, là où le PLA est très
cassant, le LW plie, ce qui le rend plus résistant aux chocs et
manipulations.
La pièce en LW est très légère et au toucher,
on dirait du papier mâché. Sa surface est granuleuse, la
structure interne se voit plus que sur la version en PLA. Les détails
sont aussi moins fins. Après peinture et décoration, le
missile a fière allure sauf à mettre le nez dessus. Pour
le mince fuseau des missiles j’ai maintenant trouvé une
technique idéale : je dessine la couleur de fond et toutes les
inscriptions de servitude, bandes colorées et détails
avec un logiciel (Illustrator) sur un rectangle dont la largeur correspond
au périmètre du tube, plus 3 mm de recouvrement. Pour
rappel, le périmètre = 3,14 x le diamètre. J’imprime
ce décor sur de l’autocollant en vinyle avec une imprimante
laser couleur. Après découpe il reste à enrouler
l’autocollant. Il adhère mal sur le matériau mais
comme il finit par se coller sur lui-même ce n’est pas grave.
L’aspect est très réaliste et parfaitement lisse,
pour une prise de masse minimale.
Au début j’ai eu un mal de chien à décoller
les pièces du plateau magnétique en acier. En pliant le
plateau, la pièce s’arrache en laissant sa base soudée
au support. Pas moyen de la récupérer, je dois la séparer
au cutter. Reste une emprunte très difficile à nettoyer.
Lame de rasoir, papier de verre ou acétone, rien n’y fait
: le LW est imprégné dans la surface comme une peinture.
Après quelques pièces mon plateau est mort, j’ai
même endommagé la couche de surface à force de gratter,
couper, poncer. J’en commande un autre de la marque "BIQU
SSS"(vendu par Kingprinter sur Amazon.de) et je mets l’ancien
au rebut. Heureusement, ce n’est pas très cher : moins
de 20 euros. Ce nouveau plateau s’avère excellent, bien
meilleur que l’original. Mais je ne l’utilise jamais pour
le LW. En effet, entre-temps j’ai découvert qu’on
peut parfaitement imprimer le PolyLight directement sur le verso du
vieux plateau, à même l’acier ! Avec un "Rim"
dans les réglages d’impression, ça marche parfaitement
pour les pièces pas trop hautes. Après refroidissement,
elles tombent toutes seules de la plaque, sans laisser de trace ! Pour
les objets hauts et étroits, ça n’adhère
pas assez et je me suis retrouvé deux fois avec une sorte de
nuage de filament pendu à la buse… Depuis, j’ajoute
sur l’acier un voile de colle en bombe (la laque pour cheveux
aurait le même effet). C’est efficace et ça se nettoie
facilement à l’acétone. Le nouveau plateau me sert
maintenant pour le PLA normal et le PETG : que du bonheur !
L’imprimante a bien tourné, j’ai imprimé
au LW toutes les charges de mon A7 Corsair II à l’échelle
1/9,5. Je vous laisse juger du résultat sur la photo, c’est
spectaculaire ! Impossible de voler avec tout ça imprimé
en PLA, la masse aurait été bien trop élevée.
J’ai aussi imprimé un petit avion et la moitié
d’un autre, de 1,24 m d’envergure. La bobine est pourtant
loin d’être vide. Le PolyLight de 3DLabPrint est donc un
choix très économique car on imprime deux fois plus qu’avec
la même quantité de PLA standard.
Ta-152 : le test ultime !
|
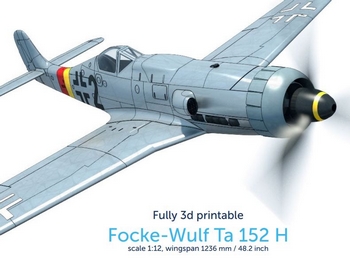 |
 |
Fort de mes succès avec le PolyLight, je décide
d’en commander une seconde bobine, de couleur balsa cette
fois. J’ajoute à mon panier un kilo de PLA spécial
"aviation" du même vendeur. Selon 3DLabPrint, le
"PolyAir" est beaucoup plus solide pour la même
masse et la même facilité d’impression que du
PLA standard. Il faut juste régler la température
à 230 degrés pour la buse et 60 degrés
pour le plateau. Notez que la firme fait régulièrement
des promotions, j’ai donc eu mes bobines à moins de
30 € pièce, ce qui est très raisonnable.
Comme l’usine se trouve en Europe (en république Tchèque),
les frais de port ne sont pas élevés et la marchandise
arrive en moins d’une semaine. Pour compléter la commande,
j’ai ajouté un chasseur de la Luftwaffe Ta-152, une
version ultrarapide du célèbre FW-190. |
Pour une vingtaine d’euros,
on télécharge un dossier avec toutes les pièces
au format "stl" ainsi que les "GCodes" prêts
à imprimer. Il n’y a pas de protection contre la
copie, le fabriquant compte sur votre honnêteté.
Inutile de me demander les fichiers, 3DPrintLab mérite
bien cette petite contribution, d’autant que le modèle
est remarquablement bien conçu, avec de nombreux détails
maquette et un beau
mode d’emploi en téléchargement libre.
Notez que si vous hésitez, ils ont aussi un petit Piper
gratuit (avec même des flotteurs !).
Tout ça est en anglais, mais c’est mieux qu’en
tchèque…
Le Ta-152 s’imprime en "PolyAir" pour les 2/3
des pièces et en "PolyLight" pour l’extérieur
des ailes, l’arrière du fuselage, le capot et quelques
détails. |
 |
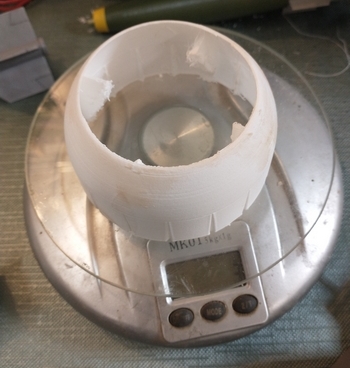 |
Je commence par la partie avant du fuselage, directement depuis le
GCode fourni (prévu au départ pour une imprimante Prusa
mais qui s’avère parfait pour l’Ender). Les pièces
finies sont superbes.
Le PolyAir est blanc translucide et effectivement solide car un peu
souple, contrairement au PLA qui est cassant à la torsion ou
à l’impact. Il ne se délamine pas du tout, les tranches
sont parfaitement soudées l’une à l’autre.
La surface comporte en outre de nombreux détails et lignes de
panneaux en creux. Ce qui m’inquiète un peu c’est
qu’il n’y a nulle part de longerons ! C’est la structure
interne qui est supposée donner la rigidité. Là,
je suis plus que sceptique. Pour le fuselage, peut-être, mais
pour cette aile démesurée ? Bon, on verra. Dans le pire
des cas, j’ajouterai un barreau de carbone…
Une semaine plus tard, l’avion est fini. Les pièces s’emboîtent
de façon diabolique et se collent facilement avec une cyano épaisse.
Contrairement à la notice, je n’ai pas utilisé de
colle fluide, qui devient cassante après un coup d’accélérateur.
Je n’ai pas renforcé les ailes, elles sont assez solides
telles-quelles, à ma grande surprise.
En revanche, l’arrière du fuselage en filament LW donne
une impression "pot de yaourt".
Pour éviter de l’écrabouiller en le prenant en
mains, j’ai ajouté des âmes en Dépron 6 mm.
La différence est flagrante, le truc tout mou devient bien rigide
et peut être manipulé sans risque, au prix de dix grammes
de Dépron.
Pour coller les âmes de Dépron, j’utilise de la
colle polyuréthane (PU). Si on y ajoute une petite goutte d’eau
ou de salive, on obtient une masse laiteuse qui gonfle énormément,
ce qui permet de fixer des pièces qui ne sont pas parfaitement
ajustées.
La mousse PU est aussi très efficace pour appliquer des congés
et renforts, ou pour combler des trous. La préparation est un
peu laborieuse car la PU est d’abord hydrophobe : on a l’impression
de vouloir diluer un chewing-gum, ça ne marche pas. Mais à
force de touiller, d’un coup le mélange se fait. On a alors
quelques minutes pour l’appliquer avant gonflage. Cette colle
est sèche au toucher après une heure et totalement durcie
le lendemain.
On ne voit pas bien l’ébauche de pilote
qui se cache dessous, mais en vol ça ne se remarque pas trop.
3DLabPrint préconise une motorisation jusqu’à
6S ! C’est monstrueusement trop pour un "warbird"
d’un kilo. Avec 300 watts il devrait déjà
bien voler. Comme j’ai un ancien moteur 1.150 kV qui tire
33A en 3S avec une hélice APC 10x5, c’est ce que je
monte dessus, après avoir imprimé le bâti en
PETG. Avec un Li-Po 2.200 mAh ça devrait être parfait.
Sur la balance, l’avion terminé et décoré
pèse 777 g tout juste. Avec l’accu il est prêt
à décoller à 960 g, soit une charge alaire
"paisible" de 45 g/dm². Même avec l’accu,
le contrôleur et le récepteur à fond en arrière,
il est toujours centré presque 1cm devant le point recommandé.
|
 |
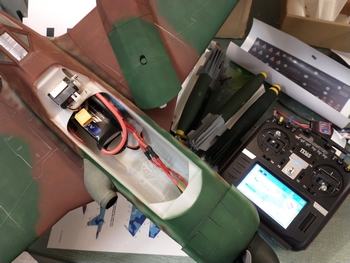 |
Comme 3DLabPrint conseille d’avancer le centrage
pour les premiers vols, je ne m’en fais pas trop. Motorisé
comme ça, l’avion tire plus que son poids à
la verticale. Aucun doute que ça sera suffisant !
Je termine le boulot avec une décoration "Avril 1945"
à l’aérographe. La peinture acrylique de la
série "XF" de Tamiya couvre parfaitement les
matériaux mais la teinte semble plus sombre que d’habitude.
J’ai peint les marques en me servant de pochoirs, les lignes
de surface et détails ont été surlignés
au crayon 2B.
Au final l’avion a fière allure. Il est déjà
assez imposant pour un modèle de moins d’un kilo.
Il n’a fallu que deux semaines de travail en soirée
pour le terminer. Rendez-vous au terrain pour le premier test. |
 |
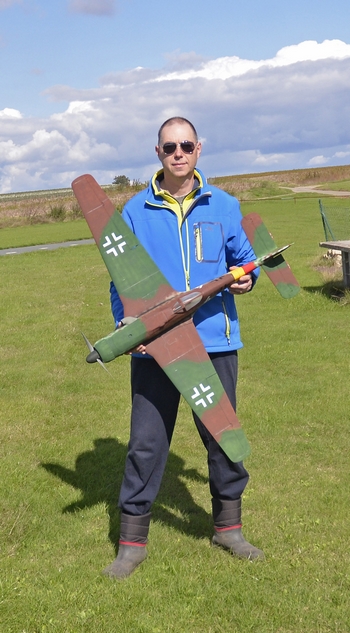 |
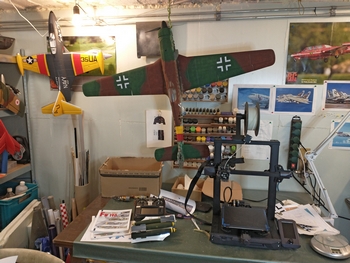 |
|
Pour ce premier test, j’ai trouvé
un volontaire pour lancer l’avion. C’est nécessaire
parce que le modèle n’a pas de train. Comme c’est
une aile basse, la bonne procédure est de le lancer "par
en bas", en prenant le fuselage d’une main au niveau
du bord d’attaque.
On peut aussi le lancer seul, sur le dos, mais pas pour un premier
vol…
A l’avenir, je lui ajouterai un crochet pour le lancer
à la catapulte. |
 |
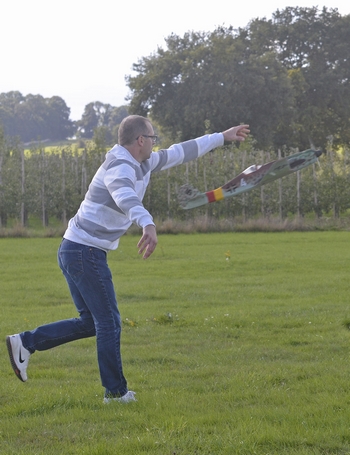 |
Je m’attends à un coup de couple vers la gauche et je
ne suis pas déçu : il part immédiatement sur la
tranche, malgré des ailerons partiellement braqués à
droite. C’est sans conséquence car le moteur est assez
puissant. L’avion prend rapidement assez de vitesse et retrouve
une assiette normale. 3DLabPrint n’a pas prévu d’anticouple
ni de piqueur mais l’avion vole droit avec la propulsion à
zéro degrés de calage. Avec l’hélice 10x5,
la vitesse n’est pas élevée, en fait c’est
très réaliste.
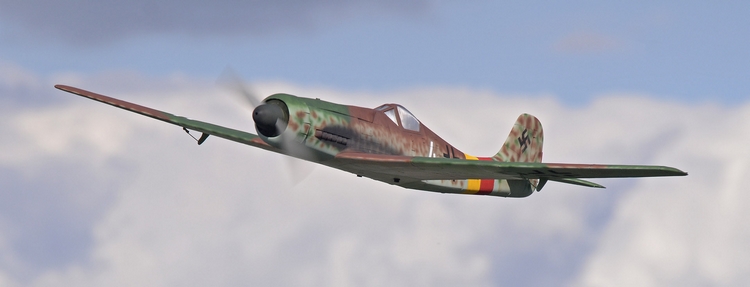 |
La traction est au rendez-vous, les loopings peuvent monter à
l’infini. Après quelques ressources et virages serrés,
mes craintes concernant l’absence de longerons et clés
d’ailes sont apaisées : il ne cassera pas tout de suite
en vol. Les débattements sont corrects. Avec ces longues ailes,
le tonneau n’est pas ultra-rapide mais confortable. Cependant,
le modèle se comporte comme si le servo de profondeur avait du
jeu ou un retour au neutre imprécis : lors d’une remise
à plat, parfois il cabre et parfois il pique. C’est désagréable
et cela nuit à la pureté des trajectoires. Après
contrôle, les commandes fonctionnent parfaitement et reviennent
exactement au neutre à chaque fois. Je soupçonne le centrage
avant de causer ce phénomène. Car en effet, l’appareil
est trop lourd du nez. Je vais devoir trouver un accu plus léger.
Je le pose après seulement 5 minutes de vol car je n’ai
aucune idée de ce qu’il a consommé. Avec sa grande
aile basse, l’avion allonge beaucoup mais à part ça
l’atterrissage est une formalité.
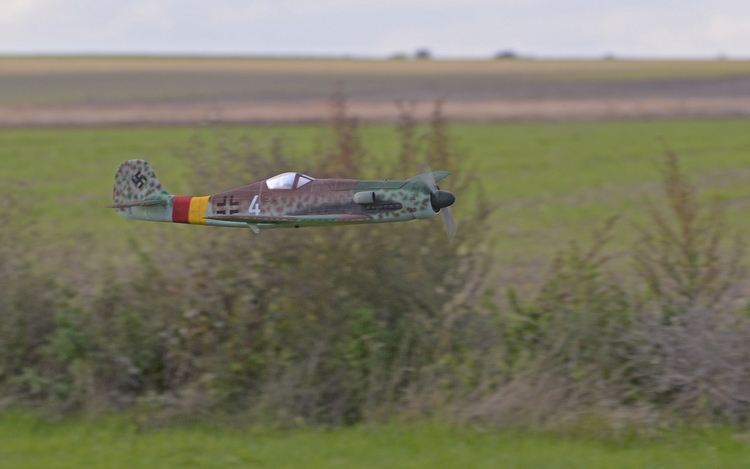 |
Le testeur d’accus annonce encore presque 60%, je pourrai donc
sans problème opter pour un Li-Po plus petit. Ou ajouter un peu
de plomb dans la queue pour ramener le CG au point indiqué par
3DLabPrint.
Après ces aventures en 3D, je dois dire
que je suis convaincu ! Les filaments PolyLight et Polyair
offrent une vraie alternative au balsa et à la mousse,
que ce soit pour des accessoires ou pour un avion complet.
Par ailleurs, le Ta-152 vendu par 3DLabPrint est un modèle
étonnant, solide et léger avec en prime un aspect
réaliste.
Si les autres avions proposés par le fabriquant sont aussi
bien conçus, je me laisserais bien tenter par le B-25 de
1,72 m, le biplan Waco de 1,44 m ou le Edge 540 de 1,85 m… |
 |
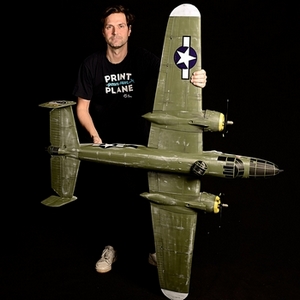 |
Les modèles imprimables en 3D vont à mon avis révolutionner
l’aéromodélisme, en offrant des appareils relativement
vite montés, originaux, performants et réparables, puisqu’il
suffit d’imprimer à nouveau la pièce cassée.
Par ailleurs, plus de risque que le kit soit épuisé :
le catalogue des avions ne cessera de grandir.
Financièrement, c’est avantageux puisqu’on peut télécharger
les fichiers pour le prix des frais de ports d’un ARF traditionnel.
L’impact pour l’environnement d’un avion imprimé
en 3D est en outre favorable, puisqu’il ne faut plus d’usines
en Asie, ni de containers maritimes pour l’envoi en Europe, de
camions pour distribuer les énormes caisses, de matériaux
d’emballage, de bois exotique, etc.
L’aspect créatif est même préservé
puisque le "maker" peut modifier les fichiers à sa
guise. Il reste aussi un minimum de montage à charge du pilote,
ce qui lui procure un meilleur "ressenti" de sa machine et
un plus grand plaisir lors du vol.
La seule inconnue concerne la tenue dans le temps des matériaux,
notamment lors des périodes de grande chaleur, car les pièces
imprimées sont connues pour se déformer au-delà
de 50°C.
Enfin, on peut espérer que cette technologie de pointe arrive
à rendre le goût de la construction et du travail manuel
que les ARF et autres "prêts à crasher" ont estompé
chez les modélistes...
Contact
: laurent.schmitz@jivaro-models.org
Ailes
brisées
(Mise à jour du 30 octobre 2022)
Après quelques vols, le
Ta-152 revient à l’atelier avec les ailes brisées…
Je voulais tester la solidité du modèle, j’ai
donc piqué plein pot puis tiré le manche à
fond pour une ressource au facteur de charge maximal. Je
croyais éventuellement perdre une aile mais la voilure
a d’abord pris plusieurs degrés de dièdre,
puis l’avion a déclenché en passant
sur le dos. La suite du vol, plus calme, a encore été
marquée par des décrochages inattendus, à
chaque « prise de G ». Après un atterrissage
normal, l’avion semble intact, je ne vois absolument
rien de spécial. Mais dès que je prends le
bout des ailes en mains, je m’aperçois que
l’intérieur est pulvérisé : les
extrémités sont devenues comme spongieuses
! Sans sa structure interne, l’aile se tord, ce qui
cause des déclenchés intempestifs.
 |
On ne voit rien de
spécial car les dégâts sont sous
la « peau » en PLA ultraléger. |
Quelques coups de cutter révèlent
l’étendue des dégâts. Le tronçon
extérieur en PLA ultraléger est le plus endommagé
: le quadrillage interne est cassé et comme cette
pièce n’a pas de longeron, elle ne tient plus
que par sa « peau ». Le tronçon suivant,
plus près du fuselage, possède un mince longeron
et a un peu mieux résisté. Clairement, la
conception des pièces en LW-PLA ne convient que pour
un vol « maquette », tranquille. Une manœuvre
brutale, même par inadvertance, risque de les endommager,
faute de renforts adéquats.
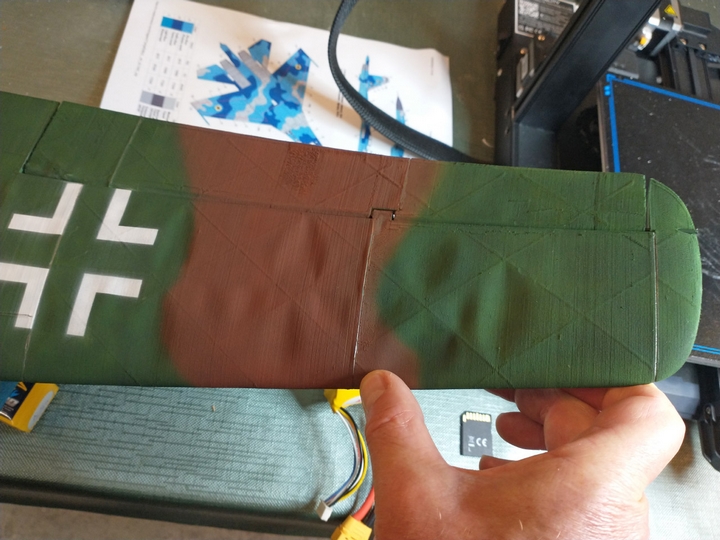 |
Les tronçons
extérieurs des ailes sont devenus « spongieux
». |
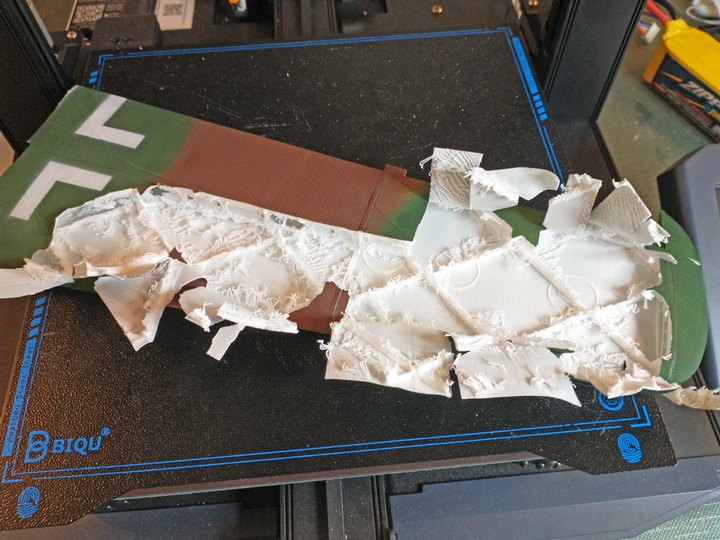 |
La structure interne
est pulvérisée. |
Si j’avais imprimé ces pièces
en PLA « Poly Air », l’avion aurait pris
quelques grammes mais les ailes auraient certainement résisté
car ce matériau est bien plus solide. Comme j’ai
téléchargé (gratuitement) l’aile
courte du modèle Ta-152C,
je décide de ne pas réparer l’aile d’origine
mais d’imprimer la version de 96 cm. Celle-ci est
plus récente et 3DLabPrint prévoit tous les
tronçons en PolyAir. Seuls les saumons et les ailerons
sont en PolyLight. Le fabriquant aurait-il connu les mêmes
déboires ?
 |
La version «
C » a le « look » inimitable d’un
« warbird » ! |
Le Ta-152C « ailes courtes » est non
seulement plus solide mais aussi plus chargé. La
vitesse augmente et avec sa faible envergure, l’avion
répond plus franchement aux ailerons. Curieusement,
le lacet inverse me semble plus important. Pour le second
vol avec cette aile, je programme donc 80% de différentiel.
Ce pis-aller aide un peu mais je continue à actionner
une gouverne de direction hélas inexistante. Le modèle
« C » n’a pas l’élégance
et l’originalité du Ta-152H aux ailes démesurées
mais il ressemble plus à un « warbird ».
Son comportement en vol est très agréable,
surtout avec un accu 1.600 mAh au lieu de 2.200, encore
largement suffisant pour 6 minutes de vol.
Finalement, pourquoi se priver ? Deux chasseurs
pour le prix d’un, c’est encore mieux ! Je vais
donc ré-imprimer une aile de type « H »,
mais cette fois avec les panneaux extérieurs en PolyAir.
|
|
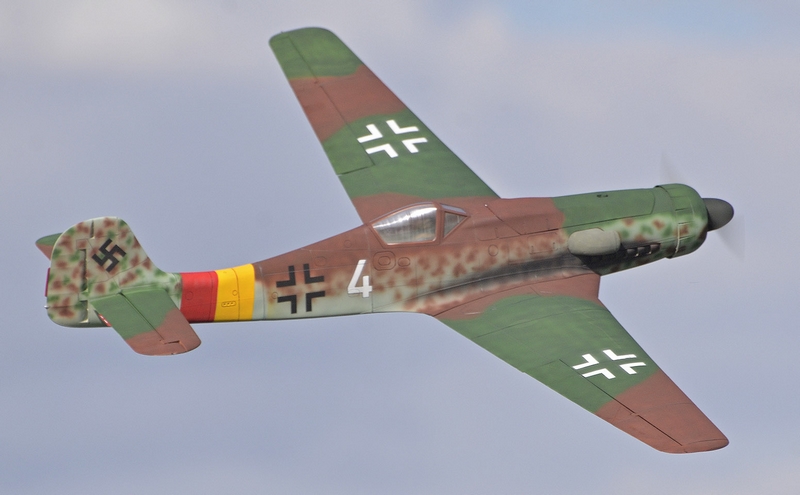 |