Présentation : Emmanuel
Elie
L'histoire
Au début était le chaos… Non, on va faire plus
simple ! 
En fait, au début était un forum avec des fous géniaux
qui se sont lancés dans l'idée que la radio Turnigy
9X, ou ses nombreux clones - je ne sais même plus qui a produit
le modèle d'origine - était suffisamment facile à
comprendre pour s'en faire une soi-même.
Tombant sur le Net sur un projet appelé Core 9X, je me suis
dit que c'était parfait pour moi comme nouveau dada. Sauf
que mes capacités à compliquer les choses allaient
m'entraîner bien plus loin… Cette petite aventure aura
été pleine d'enseignements, et je vous propose de
vous narrer ici quelques parties de ce beau voyage. |
Après un peu de lecture des forums, je réussissais sans
peine à flasher un microcontrôleur - c'est le nom de ces
circuits intégrés mystérieux, noirs, carrés
et plein de pattes, véritable cœur du système. La
cible, un ATMega128 que j'avais soudé, avec un peu plus de peine
(qu'elles sont petites ces pattes), à une carte très minimaliste.
Encore dépourvue d'organe de commande, cette mini radiocommande
m'offrait peu de preuve d'affection en retour. Il faut dire que sans
écran, j'avais quelques difficultés à dialoguer
avec mon œuvre. J'avais des écrans en stock, mais sans les
connecteurs adaptés ni beaucoup de connaissances sur leur mise
en œuvre. Bref j'avançais lentement.
Les difficultés avec les écrans et un goût prononcé
pour faire plusieurs choses à la fois, toutes passionnantes et
essentielles bien sûr, ont fait que le projet a traîné
et enfin dormi dans un fond de tiroir.
Puis je suis tombé sur le site d'un autre individu génial,
connu pour ses conceptions aérodynamiques innovantes et performantes
de planeurs, j'ai nommé monsieur Franck Aguerre. Il donne toutes
les indications pour se faire une radio complète et extrêmement
performante, inspirée du projet Core 9X, mais pour un résultat
de bien meilleur niveau.
Le projet se nomme NextStep RC. Il y a un site magique et un forum formidable
qui va avec, le tout se retrouve dans le chapitre « liens
» en fin de ce texte.
Tous y est repris, détaillé et expliqué pour que
chacun puisse se faire SA super radiocommande qui fait tout super bien.
Que Monsieur Franck Aguerre soit ici mille fois remercié, il
m'a remis le pied à l'étrier.
Le reste de ce texte pourrait paraître un peu obscur à
ceux qui n'auraient pas encore cherché leur chemin dans un projet
comparable. Quelques termes barbares émaillent les échanges
entre spécialistes. Pour l'instant, je ne vous ai asséné
que le « ATMega128 ». Je conseille donc TRES vivement de
commencer par le site de maître Franck Aguerre, qui a, entre autres
qualités, le bon goût d'être en français.
J'ai une Turnigy 9X reflashée, donc compatible avec le
logiciel OpenTX qui est au cœur du projet NextStep RC. Je fais
du planeur et j'essaye toujours de prendre le minimum de place
dans la voiture familiale ou le sac à dos pour le matériel.
J'ai envie de tenter le lancé-main dont le geste auguste
appréciera un boîtier pas trop gros.
J'ai de multiples modèles, mais pas tous équipés
de la même technologie de récepteurs. Il y a principalement
du Turnigy et du Assan.
Il me reste un cadavre d'émetteur
WFly WFT08 dont toute la mécanique est très bonne.
Donc je vais me faire un émetteur compact
multi-protocole, et qui pourra faire écolage avec ma 9X.
Pour ce faire, la partie écran et boutons
de navigation/programmation sera sur un boîtier détachable
connecté en façade. Pour connaître l'état
de la radio sans écran lorsque ce dernier sera déconnecté,
on s'offre l'option synthèse vocale. Et oui, ça
aussi c'est possible.

|
 |
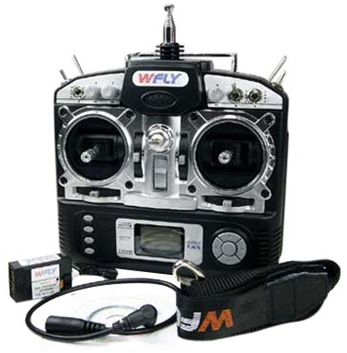 |

|
 |
Le boîtier de la WFT08 sera
recoupé en partie basse (en fait tout ce qui est noir sous
les manches). Un nouveau boîtier est donc à concevoir
en partie basse, et puisque le module multi-protocole qui sera
utilisé n'est pas compatible avec la carrosserie de la
WFT08, il faudra aussi refaire un dos de remplacement.
 |
On retaille un peu la
platine porte-interrupteur de la WFT08 et on constate qu'il reste
de la place pour un petit module de type Arduino Mega2560 Pro
Mini.
En partie haute du boîtier de la WFT08, une
fois enlevée une tige support de la carte interrupteur,
on logera aisément un haut-parleur et sa carte de synthèse
vocale.
|
 |
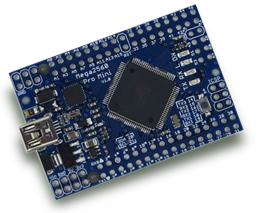 |
Rien, mais alors rien d'original par rapport au projet NextStep
RC. On fait tout comme le maître il a dit, et si ça ne
fonctionne pas, on reprend tranquillement les explications données
pour les suivre dans l'ordre.
Ma particularité est de plus souvent être sous Mac que
sur PC, ce qui impose parfois de trouver quelques alternatives.
Par exemple, pour flasher ma carte Mega2560 via l'interface série
et les broches MOSI/MISO/etc., je voulais utiliser le logiciel Companion,
qui accompagne le logiciel OpenTX pour la radio. Companion me dit qu'il
fait tout bien, mais ça ne donnait rien. En cherchant, j'ai constaté
qu'il n'écrivait pas vraiment dans la mémoire de la carte.
Sans réussir à lever le mystère du pourquoi, j'ai
contourné en passant par le logiciel HexUpoader, ce qui m'offre
en plus l'élégance d'une communication via le port mini
USB de la carte. Exit les fils et soudures supplémentaires pour
l'interface série câblée, ainsi que le besoin d'une
prise de programmation faite maison.
|
Alors que ma vieille Turnigy 9X utilise
une prise de type DIN, des fils soudés sur la carte mère,
et un adaptateur USBasp au bout d'une longue nappe plate, ma nouvelle
radio communiquera donc en USB avec un câble disponible
chez tous les revendeurs d'accessoires pour téléphone.
C'est quand même plus simple avec un câble
standard non ?

|
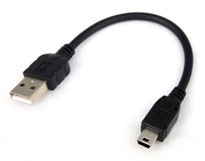 |
Le
câblage : faire propre |
Ayant quelques réalisations électroniques à mon
actif, je sais que c'est lors des manipulations, montages et démontages,
que nos beaux projets défaillent lentement, car les fils, trop
malmenés, les soudures, mal protégées, subissent
des contraintes mécaniques néfastes à leur survie.
Donc pour commencer, on part sur une simplification et fiabilisation
du câblage de la WFT08 qui, d'origine, a des fils tous individualisés
et repris, via de multiples connecteurs, sur la carte interrupteurs
et sur la carte mère.
Les points communs des interrupteurs à relier à la masse
sont tous sériés l'un après l'autre par des fils
assez longs pour être placés dans le boîtier mais
assez courts pour ne pas se prendre dedans. J'ai réutilisé
pour cela les excellents fils à gaine siliconées d'origine
de la WFT08. Marron pour la masse, blanc pour le plus.
Même punition pour les fils extrêmes, la masse et le plus,
des boutons de trims et des potentiomètres des manches. Attention
à penser aux débattements des manches pour le placement
et la longueur des fils.
Lorsque c'est fait, on vérifie au multimètre la qualité
de chaque connexion, puis on immobilise chaque fil autour de chaque
soudure d'une goutte de colle néoprène qui recouvre la
soudure et le début d'isolant du fil. C'est fait pour ne plus
jamais y toucher.
On se dote ensuite d'un bon fil de câblage fin et de couleurs
multiples. J'avais pour cela un câble rond multiconducteurs, tous
multibrin à gaine téflonnée. C'est juste parfait.
Surtout pas de fil rigide (monobrin) incapable de résister aux
manipulations, ni de fil à l'isolant trop rigide pour les mêmes
raisons.
Chaque point signifiant, interrupteur, milieu des trims et potentiomètres
de manche se voit doté d'un fil de couleur spécifique,
sécurisé comme les autres à la colle néoprène.
On continue par la création de deux mini-nappes multicolores,
une de 3 fils pour le module radio, et une de 4 fils pour le module
de synthèse vocale.
Il faut aussi prévoir les câbles pour raccordement d'une
batterie d'alimentation avec son connecteur, et prévoir un connecteur
intermédiaire pour que la carte Mega2560 puisse rester démontable
sans couper de fil.
Sur la carte Mega2560 Pro Mini, j'ai soudé une barrette coudée
double mâle pour recevoir tous ces fils, et confectionné
deux connecteurs femelle à partir de deux rangées de bons
connecteur (j'insiste, des bons). Reste à souder un par un ces
fils en prenant soin d'y enfiler au préalable un petit bout de
gaine thermo-rétractable. Une fois tout soudé et vérifié,
on rétreint les gaines thermo-rétractables, on façonne
à chaud la nappe de fil pour donner l'orientation, puis on fixe
le tout avec quelques gouttes de colle au pistolet chaud et des colliers
rapides. Là non plus, on n'y touchera plus.
Côté carcasse de la radio, avec la carte de synthèse
vocale en place, tenue au double-face épais, et son haut-parleur
associé, maintenu par un jeu de taquets en bois, cela donne ça
:
Pour l'écran et les boutons, j'ai opté pour une connectique
type HE10, avec 26 contacts. La partie mâle reste sur l'émetteur
et est raccordée, en fil à fil, à la carte Mega2560.
C'est un petit jeu de patience, entre l'ajustement de la bonne longueur
de chaque fil, le petit bout de gaine thermo-rétractable côté
connecteur, et les soudures sur la carte et le connecteur. La nappe
ainsi réalisée est sécurisée sur la carte
Mega2560 par un collier rapide passé par un trou présent
fortuitement sur la carte.
La partie femelle HE10 reçoit une nappe multicolore de 26 conducteurs,
je n'en utiliserai que 23. L'autre bout de la nappe est soudé
sur le connecteur-écran et les boutons. Attention à ne
pas prévoir une nappe trop longue, la perte en ligne ou la capacité
engendrée par la nappe est néfaste au bon fonctionnement.
A partir de là, on branche tout et on alimente la carte Mega2560
par son port USB et… miracle, ça marche !
Comme indiqué plus tôt, l'intention est de refaire un
boîtier pour la partie basse et la partie arrière, plus
un boîtier déporté pour les boutons et l'écran.
N'ayant jamais fait de conception ni d'impression 3D, je m'y suis lancé
avec fougue et naïveté. C'est là que ça s'est
corsé...
Mon idée initiale, je devrais dire mon fantasme, était
de trouver un scanner 3D, de scanner mon boîtier actuel, puis,
« tout simplement » de le modifier informatiquement
pour le plier à mes envies.
J'ai rapidement compris que ce ne serait pas possible et qu'il fallait
dessiner la totalité du boîtier en partant de rien, ou
pas grand-chose, dans un logiciel de conception en 3D.
Le logiciel utilisé est DesignSparkMechanical mais il en existe
pleins d'autres, tous avec leurs qualités et défaut, limites
en termes de possibilités, ou bugs dans les algorithmes.
Le plus délicat est la prise en main et la conception de la pièce
à réaliser en fonction des possibilités du logiciel.
Par exemple, celui que j'ai retenu ne sait pas faire une pièce
par symétrie miroir d'une première pièce ! D'autres,
tel PCon, par exemple, font cela instantanément. D'autres travaillent
dans un format de fichier un peu trop propriétaire, qu'il devient
délicat d'exporter vers l'imprimante 3D.
Pour l'impression 3D, j'ai eu accès au LabFab du
Pôle Numérique Rennes Beaulieu et aux conseils avisés
de Laurent Mattle, un autre monsieur essentiel à ce projet. Le
matériel disponible utilise le logiciel UltiMaker Cura qui digère
des fichiers STL, lesquels fichiers sont nativement exportables depuis
DesignSparkMechanical.
Par tâtonnements et expérimentations successifs, j'ai
accouché d'une conception satisfaisante à mes yeux.
Chacun pourra la reprendre ou la modifier à loisir suivant ses
besoins, les fichiers sont mis en partage dans ce but.
Tout d'abord, pour se faire la main, le boîtier de déport
des boutons et de l'écran. Le principe est celui d'une
petite console autonome, qui réutilise deux boutons et le capuchon
de joystick d'une manette inutilisée qui passait par là.
La pièce maîtresse est l'écran autour duquel
toute la conception est faite pour le maintenir par emboîtement
sans jeu.
Pour être honnête, la précision d'impression
3D employée est de 0,6 mm. Bien moins précis que ma conception
par ordinateur. En conséquence, il reste de l'ajustage
à faire à la main pour que la pratique rejoigne la théorie.
Les fichiers proposés tiennent compte des constats faits, mais
je n'ai pas imprimé de nouvelles pièces depuis lors
pour valider les modifications.
|
 |
De plus, le niveau de finition des
surfaces en impression 3D était assez moyen. J'avais même
de gros défauts sur la face avant du boîtier. Huile
de coude et papier abrasif ont donc été à
l'honneur.
Heureusement, le plastique utilisé, le PLA,
se ponce bien pour peu que la finition soit soignée au
grain 500 ou même 800.
Après peinture et verni, le résultat me plait
assez pour le montrer.
 |
 |
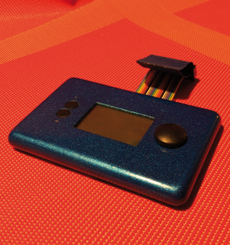 |
Il reste à marquer les boutons EXIT et MENU, le procédé
d'impression 3D ne l'ayant pas permis car directement sur la face qui
sert de base à l'impression. Cette face est constituée
d'une sorte de « flaque » de PLA, plus large que le design
à imprimer, pour bien le maintenir collé au plateau le
temps de l'impression. Je découvrirai plus tard, que l'on peut
parfois se passer de cette flaque d'adhérence au plateau d'impression.
On ne s'arrête pas en si bon chemin, au tour du boîtier
inférieur et du dos de la radio.
La partie inférieure reçoit un logement solide pour le
connecteur HE10, avec 2 volets articulés pour pouvoir limiter
l'entrée de poussières. Elle intègre aussi un support
pour les batteries et un support pour la carte Mega2560 avec le trou
pour la prise mini USB.
Le dos doit surtout s'ajuster sur la face avant de la WFT08 d'origine,
avec les fixations par 2 vis à cette face avant, et recevoir
le module d'émission multiprotocole, tout en offrant une bonne
prise en main. Il y a aussi un trou en position supérieure gauche
pour un contacteur qui permettra au choix de laisser la main à
un élève en situation d'écolage, ou de maintenir
le mode de vol « launch » pour le lancé-main.
Dans les deux cas, le gros chalenge, c'est qu'on doit s'ajuster à
la géométrie existante de la face avant de la WFT08 recoupée.
Pour cela, l'astuce (merci Laurent Mattle), est de passer cette face
avant dans une grosse imprimante scanner pour en numériser les
contours.
On passe à l'encre blanche (ou peinture, ou correcteur liquide…)
le champ du boîtier que l'on veut scanner, et avec un peu de travail
de l'image, on obtient des contours assez contrastés pour les
reprendre avec un logiciel de dessin vectoriel. On s'assure de la bonne
mise à l'échelle, on importe dans le logiciel de conception
3D. On tâtonne, on recommence, et finalement, on obtient un chemin
sur lequel s'appuyer pour commencer la conception en volume.
Après quelques heures de travail passionnant (mais si, mais si),
où l'on apprend le B-A-BA de la modélisation dite paramétrique,
on obtient cela sans avoir besoin d'être un pro :
Je trouve ça beau, mais je ne suis probablement pas objectif.
Note aux benêts comme disait un copain, le dos existe en 2 versions
et plusieurs fichiers d'impression. Les deux versions, parce que j'ai
un peu galéré pour arriver à mes fins. La version
1 est imparfaite mais en 1 seul morceau, la v2 est bien mais la conception
est en plusieurs bouts. Les fichiers séparés d'impression
car, en fonction de la capacité de votre imprimante à
gérer la complexité des formes, il peut être utile
de séparer :
• Une partie principale imprimée debout (en rose sur l'image
précédente).
• Une partie « casquette » à imprimer à
plat sur son dos (bleu ciel).
• Un complément à la casquette pour fermer l'extérieur
du logement du module RF (bleu marine) et solidarisé par deux
rivets de 3 mm de diamètre (à imprimer pleins pour une
résistance satisfaisante).
Ce dos m'aura causé pas mal de soucis. Difficulté de modélisation
d'abord. Difficulté d'impression, avec en plus, un changement
de machine en cours de route, mais j'y reviens plus loin.
Et oui, les premières pièces imprimées ne s'ajustaient
pas bien, mais, plus encore, la technique d'impression générait
des défauts.
D'une part toutes les surfaces en surplomb se retrouvent dans le vide
pour l'impression, ce qui provoque des défauts avec des filaments
qui sont mal collés car appuyés sur du rien ou presque
rien. Pour y remédier, je créé un maximum de pentes,
autour de 30 degrés pour limiter les surfaces horizontales lorsque
c'est possible. Des congés et des plans de joint aident aussi
à limiter cela.
D'autre part, je limite les grandes surfaces épaisses tant que
possible sur le plan de départ, ayant constaté des défauts
de décollement sur ces surfaces et des effets de déformation
au refroidissement.
Enfin j'évite de démarrer l'impression sur une courbe,
genre cylindre couché, car alors de grandes quantités
de plastique sont consommées pour supporter la matière
au point de tangence avec le plateau d'impression.
Ce qui conduit, pour le dos, à l'imprimer verticalement, et pour
le bas, à un design en 2 parties qui s'imprimeront tête
bêche, avec le plateau de départ comme plan de jonction.
Toutes les pièces sont imprimées en pas fin de 1/10e par
couche et avec un taux de remplissage à 17%, sauf les rivets
qui sont totalement pleins.
Voici les pièces en configuration d'impression.
La
carrosserie, deuxième épisode |
Les vacances sont terminées. Les températures sont encore
très agréables pour moi qui aime la chaleur. Un peu moins
agréable si l'on pense au réchauffement climatique dont
cela démontre la réalité, n'en déplaise
au gros bébé roux d'outre atlantique.
Quel est le rapport avec notre projet ? Il est mince, mais c'est parce
que nous imprimons souvent avec du PLA, matériau plastique que
je préfère à l'ABS car il est recyclable et biodégradable.
J'avais donc acheté du PLA, mais, distrait, je n'avais pas fait
attention qu'il existe en plusieurs diamètres et m'était
doté d'un magnifique bleu en diamètre 1,7 mm.Or l'imprimante
UltiMaker utilisée jusque-là est configurée pour
du 3 mm. Diantre, palsambleu, peste, que faire de mon PLA bleu ?
La réponse fut le prêt généreux par Laurent
M d'une imprimante Dagoma DiscoEasy200, montée par des étudiants
et que j'avais donc charge de régler en contrepartie.
La DiscoEasy200 est une imprimante 3D de qualité tout à
fait satisfaisante, quoiqu'un peu susceptible, mais proposée
en kit dont plusieurs pièces sont réalisées en
impression 3D. Oui, la guerre des clones a déjà commencé,
des imprimantes fabriquent des copies d'elles-mêmes.
Cette imprimante accepte par défaut du PLA en 1,7 mm, et est
associée à une déclinaison spécifique et
simplifiée du logiciel "Ultimaker Cura" ou "Cura".
Autre différence, le plateau d'impression est très lisse
et doit être recouvert d'un revêtement pour y faire adhérer
les impressions. Le revêtement conseillé pour débuter
est un simple scotch de masquage de couleur bleue, plutôt bien
adhérent. L'intérêt, c'est qu'il n'est plus besoin
d'une première couche plus large qu'il faudra éliminer
ensuite par ponçage (la flaque évoquée plus tôt).
On peut donc obtenir des pièces presque prêtes à
l'emploi, y compris avec des parties creuses sur le premier plan imprimé,
tant que la surface en contact avec le plateau offre assez de résistance
pour tenir les contraintes de ce qui sera imprimé au-dessus.
Ainsi, dans la réalisation de la partie basse du boîtier,
la zone porte-piles commence en particulier par 2 petits plots qui s'évasent
rapidement pour rejoindre le reste du boîtier. Ces petits plots
sont trop petits pour résister dès que l'on arrive à
plus d'1 mm de couches. J'ai donc intégré un petit plateau
juste pour eux dans mon design. Ce sera la seule partie à éliminer
avant assemblage.
L'imprimante de Dagoma ne comporte pas de support pour la bobine de
filament. Lorsque que j'ai lancé ma première impression,
j'ai déroulé dans la pièce une grande longueur
de filament. J'ai surveillé le bon déroulé du début
de l'impression, puis je suis allé dormir sur mes deux oreilles.
Au réveil, j'ai constaté
que le filament avait fait un nœud, qui avait bloqué
sa progression, et qu'il manquait un peu moins de 2 mm d'épaisseur
pour finir la pièce. C'est ballot ! Plutôt que de
réimprimer, et parce qu'il s'agissait de terminer le dessous
presque cylindrique du boîtier, j'ai puisé dans ma
boîte à chutes, trois baguettes de bois dur pour
finaliser cela par une touche de marqueterie assemblée
à l'époxy et poncée sur pièce. Ainsi,
je n'aurais pas gâché de matière. Le reste
des impressions se fera avec un petit support maison qui remplit
parfaitement son office.
Vue sur le support, fait de planchettes et d'un
tube qui traînaient par là. Une fois enfilé
sur le tube, le rouleau de filament se dévide sans heurt.
|
 |
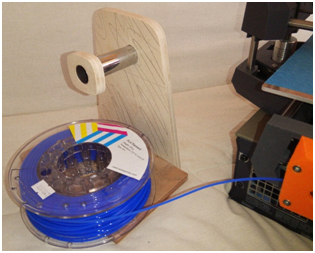 |
Les deux morceaux de la partie basse du boîtier sont assemblés
aussi à l'époxy. La précision est un peu imparfaite.
Pour les trous de 6 mm qui doivent permettre d'aligner les deux
morceaux, j'utiliserai finalement deux forets de 5,5 mm dont je dispose
plutôt que d'ajuster les trous. Pour le plan de jonction, la continuité
du bossage frontal est perfectible, mais j'avais prévu un peu
de ponçage sur cet ensemble. Un coup de papiers abrasif 120,
250, 500 et 800 pour que ça me plaise assez. Un peu de fond dur
appliqué au chiffon et ça brille tout en finissant bien
le ponçage du PLA et du bois. J'aime bien le résultat
final.
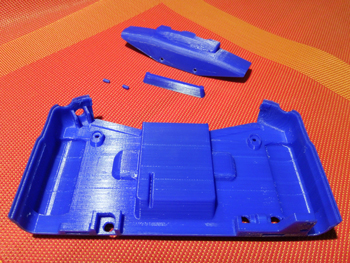
|
 |
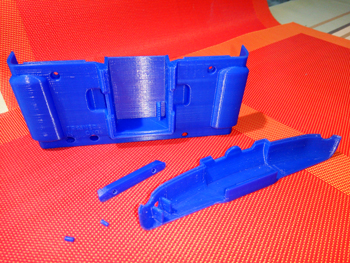 |
Puzzle du dos du boîtier.
A gauche, la version 2. A droite, la version 3. |
La vue de dessous, avec le raccord
en marqueterie et la prise mini USB.
Enfin l'emplacement de la carte Arduino Mega2560
Pro Mini est ajusté à la micro-lime plate, ou, à
défaut, avec un papier abrasif sur une (vieille) carte
de crédit.
La partie dos du boîtier sera laissée brute d'impression.
Seule la casquette, si elle est imprimée séparément,
peut nécessiter de casser l'angle au contact avec le plateau.
J'aime assez le look apporté par l'empilement des couches.
En plus, ça fait un peu grip pour la prise en main. Il
reste à assembler le tout.
|
 |
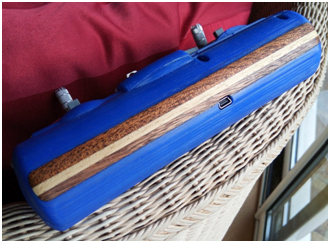 |
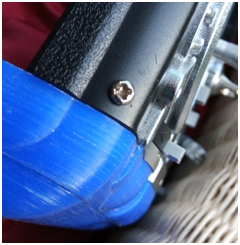
|
 |
On peut donc commencer à
assembler. Le bas est solidarisé de la face avant par deux
vis. On présente les deux parties, on perce en biais au
travers de la face avant et du bloc de maintien de la partie basse.
On pose la première vis, puis on répète avec
l'autre côté. C'est fait pour rentrer légèrement
en force.
Ci-contre, détail d'une des deux vis.  |
La batterie est mise en place dans la partie basse. Je la maintiens
avec un serre-câble velcro collé dans le fond du boîtier,
la place est prévue pour. Puis le dos est équipé
du connecteur pour le module HF et du dernier interrupteur. J'ai fait
la jonction électrique avec la face avant via un simple connecteur
2 contacts de type barrette.
Viennent ensuite les deux Jack d'écolage et la prise de recharge,
qui restent amovibles. Et le dos se place naturellement, emboîté
sur les deux tenons rectangulaires du boîtier bas, puis solidarisé
par deux vis aux emplacements exacts du boîtier d'origine.
Lorsqu'imprimé en plusieurs morceaux, les collages méritent
un peu de précision pour un beau résultat final, mais
comme on dit maintenant, ça le fait.
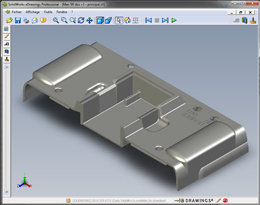 |
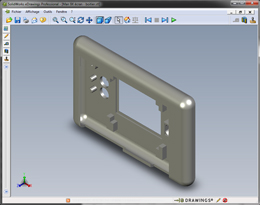 |
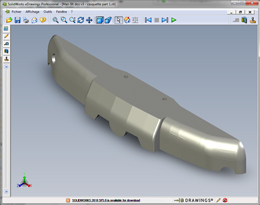 |
Les fichiers au format STL
directement exploitables pour l'impression 3D sont téléchargeables
en cliquant sur ce lien (9,7 Mo). |
Petit
complément pour l'impression et ses difficultés |
Un mot sur l'impression
du dos avec la Discoeasy200. Autant l'imprimante Ultimaker avait
sorti un premier prototype de qualité satisfaisante, autant
là, j'en ai bavé pour sortir une pièce potable.
La première tentative a fait apparaître plusieurs
défauts. Le premier, ce sont des gouttes noires de PLA
carbonisé. C'est le signe de fuite de PLA dans la tête
d'extrusion, lequel coule sur la pièce après avoir
été trop durablement chauffé. Ce défaut
ne doit pas apparaître sur une imprimante non brutalisée,
les têtes étant généralement livrées
assemblées.
Aussi, j'ai eu un décalage
progressif des couches vers le haut, suivi longtemps après
d'un décalage massif en Y, et d'une redescente de la tête
jusque dans le plateau, ainsi que de nombreux bouchages de la
buse.
Là, c'est la durée d'impression qui pose problème.
En effet, pour la buse qui se bouche, la tête chauffe trop
et le PLA en fusion finit par remonter trop haut dans la tête
d'impression. Une masse de PLA se forme alors qui colle trop aux
parois de la tête, ce qui bouche le tout car l'extrudeur
n'arrive plus à pousser (et ça c'est TRES pénible).
Les décalages sont dûs à une surchauffe des
contrôleurs de moteurs pas à pas qui perdent de leur
linéarité et finissent par se mettre en sécurité.
Les solutions ont étés
multiples :
- • Remontage soigné
de la tête d'impression. J'ai même refait le pas
de vis du bloc aluminium de la hotend pour un serrage propre
et étanche sans effort exagéré au serrage.
• Utilisation de pâte silicone, appelée aussi
compound pour radiateurs en électronique, sur le pas
de vis du radiateur de refroidissement, pour une bonne conduction
de la chaleur.
• Pose d'un radiateur sur les drivers de moteur pas à
pas, toujours avec la pâte silicone. A posteriori, je
pense qu'on peut s'en passer car le problème principal
est le suivant :
• Mise
en courant d'air frais de l'imprimante pendant l'impression,
ce qui permettrait probablement aussi de se passer du radiateur
sur les drivers. Ça c'est le remède miracle. Visiblement,
le ventilateur de la tête d'impression semble, en effet,
bien à la peine.
En plus, j'avais un décollage
des angles, et ai donc adopté une technique radicale. La
combinaison du paramètre « augmentation de la
surface d'adhérence » (petite flaque de PLA à
la première couche), et l'usage d'un double-face mince
à moquette sur le plateau, comme surface de départ.
Pas facile de récupérer sa pièce mais on
y arrive. |
Au final, je ne regrette pas l'aventure, même si j'ai choisi
la voie difficile du boîtier3D sur base d'un existant.C'était
volontaire, et j'ai appris plein de choses. Je dispose maintenant de
l'émetteur que je voulais, compact, parfaitement compatible avec
mon parc de modèles et mon autre radio.
Surtout, si vous vous lancez et souhaitez utiliser mes fichiers, allez-y,
c'est fait pour.
Contacter l'auteur : manu@jivaro-models.org